Table of Contents
In modern manufacturing, machining accuracy is a key factor in ensuring part quality, optimizing productivity, and controlling costs.
With the development of high-end manufacturing, machining accuracy has significantly improved.
It has advanced from the traditional millimeter level to the micron level, and even the nanometer level.
This leap in precision provides strong technological support for industries such as aerospace, semiconductors, and medical devices.
Machining accuracy is mainly used to produce the degree of product; machining error and machining accuracy are both terms used to evaluate the geometric parameters of the machined surface.
Machining accuracy is measured by tolerance grade. The smaller the grade value, the higher the accuracy.
On the other hand, machining error is expressed by a numerical value. The larger the value, the greater the error.
A high machining accuracy means a small machining error, and vice versa.
Some beginners may not have a relatively straightforward concept of this. This article will provide a detailed introduction to some basic and essential knowledge.
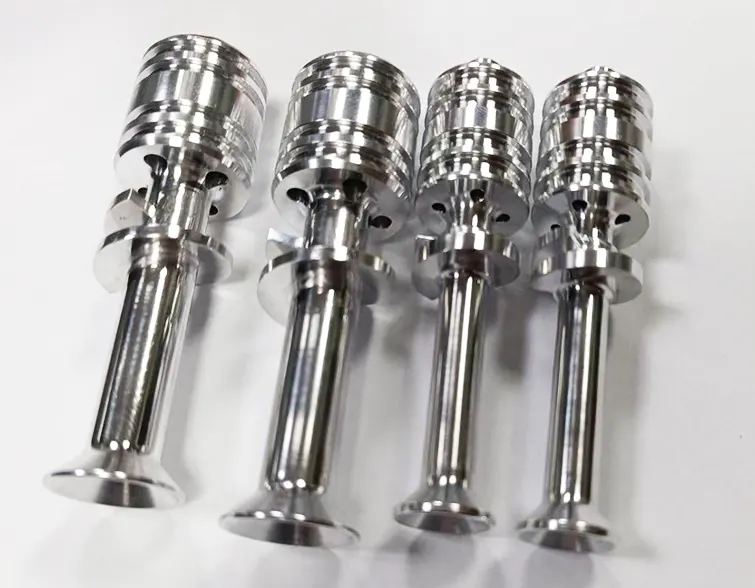
Why do we need to classify the machining accuracy level?
The specific reasons are as follows:
Adapt to different product requirements
Different products or parts have different requirements for machining accuracy, for example:
General mechanical parts (such as racks and brackets) require lower precision requirements and can be machined using ordinary techniques (0.1mm ~ 0.05mm).
Precision instrument parts (such as molds and aerospace components) require high-precision machining (0.01mm ~ 0.001mm).
Optical and semiconductor devices require ultra-precision machining (0.0001mm level).
Dividing the precision level allows you to choose the appropriate machining method for different application scenarios.
Reduced machining costs and increased productivity
The higher the machining accuracy, the higher the equipment requirements, the higher the tool wear, and the higher the cost:
Rough machining (e.g. ordinary milling, drilling) removes material quickly and at low cost.
Finishing (such as precision boring, grinding) time is long, but can ensure dimensional accuracy.
Ultra-precision machining (e.g. mirror grinding, nano-machining) requires expensive equipment and has the highest cost.
By reasonably selecting the precision level, the processing cost can be reduced, and the efficiency can be improved, all while meeting the requirements.
Ensure assembly precision, improve product quality.
The machining accuracy of mechanical parts directly affects the assembly accuracy, for example:
The fit of shafts and holes requires appropriate tolerances (e.g. H7/g6).
Precision mold cavity processing accuracy determines the consistency of plastic parts.
Too high or too low precision will affect product quality. For example, too loose a tolerance will lead to a loose assembly, while too tight a tolerance may lead to assembly failure.
Selection of suitable machining equipment
Ordinary machining (CNC milling, ordinary turning) can be accomplished with conventional CNC machines.
High-precision machining (precision grinding, five-axis machining) requires high-end CNC equipment, such as high-precision five-axis machine tools and precision grinding machines.
Ultra-precision processing (optical processing, ultra-precision boring) requires ultra-high-precision machine tools, such as nanoscale grinding machines and ultrasonic processing machines.
Classification of precision levels helps to rationalize equipment arrangement and improve production capacity.
Quality control and standardization
Dividing the machining precision grade can help enterprises establish quality standards, such as:
To control dimensional tolerances, conform to international standards (ISO 2768, DIN 7168, GB/T 1804).
In short, the division of machining accuracy grades arises from practical needs in actual work.
To understand its importance, we must reflect on the journey taken by the pioneers of the Industrial Revolution.
Through their long path of exploration and progress, we realize how essential precision truly is.
How is machining accuracy divided?
Tolerance grade is used to determine the level of dimensional accuracy.
According to the national standard, tolerance grades are divided into 20 levels, ranging from IT01, IT0, IT1, IT2 to IT18. The larger the grade number, the lower the tolerance level and machining accuracy.
A higher grade number also means a more extensive allowable range of variation, known as the tolerance value. As the tolerance value increases, the part becomes more challenging to process accurately.
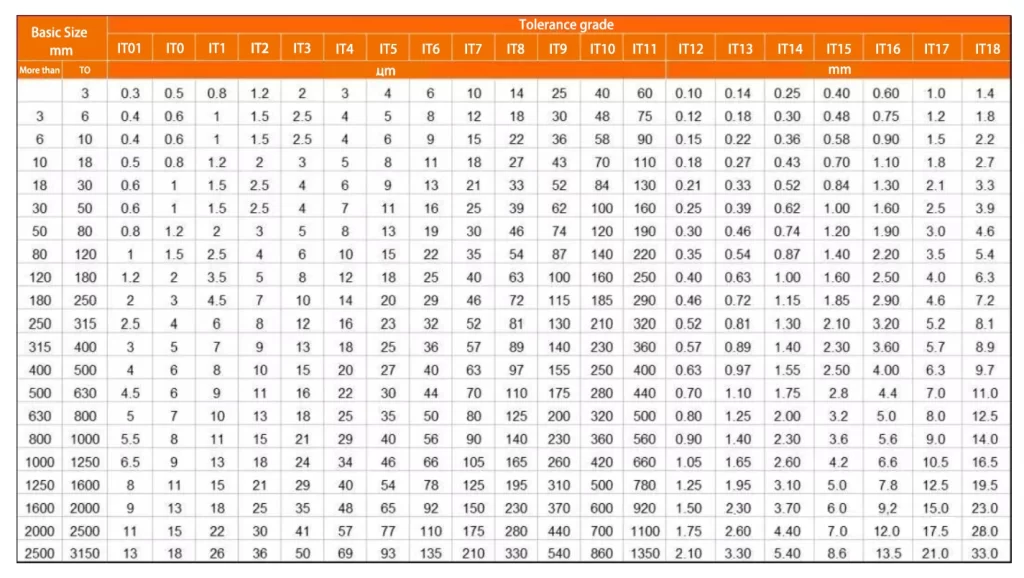
The machining accuracy of CNC machining can be generally classified according to the following levels:
Rough Machining
Accuracy range: 0.1mm or more
Surface roughness: Ra 12.5μm or more
Applicable scenarios: preliminary machining, removal of most of the residual quantity, and parts with low precision requirements.
Semi-Finish Machining
Accuracy range: 0.05mm to 0.1mm
Surface roughness: Ra 3.2~6.3μm
Applicable scenarios: Preparation for subsequent finish machining to improve the accuracy of the shape and size of the part.
Finish Machining
Accuracy range: 0.01mm to 0.05mm
Surface roughness: Ra 0.8 to 3.2μm
Applicable scenarios: to achieve the part’s final size and tolerance requirements and ensure assembly accuracy.
High Precision Machining (High Precision Machining)
Accuracy range: 0.001mm to 0.01mm
Surface roughness: Ra 0.2 ~ 0.8μm
Applicable scenarios: high precision parts, such as precision molds, aerospace parts
Ultra-Precision Machining
Accuracy range: Less than 0.001mm (1μm or less)
Surface roughness: Ra 0.01 ~ 0.2μm
Applicable scenarios: Optical parts, semiconductor devices, core components of precision instruments.
The actual parameters obtained by any processing method will not be accurate.
From the viewpoint of the function of the part, as long as the processing error is within the tolerance required by the part drawing, processing accuracy is guaranteed.
Difference between accuracy and precision:
1, accuracy
Refers to the degree of proximity between the measurement results obtained and the true value.
High measurement accuracy means that the systematic error is small. In other words, the average value of the measurement data deviates less from the true value.
However, if the data points are scattered, it indicates that the size of the random (or chance) error is uncertain.
2、Precision
Refers to the reproducibility and consistency between the results obtained from repeated measurements using the same alternate sample.
It is possible for a measurement to have high precision but low accuracy.
For example, consider a standard length of 1 mm. If the three measurement results obtained are 1.051 mm, 1.053 mm, and 1.052 mm, the results are very close to each other. This indicates high precision.
However, the measurement is inaccurate since they all deviate from the true value of 1 mm.
Accuracy indicates the correctness of the measurement results, while precision indicates their repeatability and reproducibility. Precision is a prerequisite for accuracy.
Machining accuracy and surface roughness of each process
Product parts according to the different functions, the need to achieve different machining accuracy, the choice of machining forms and machining processes are different.
This article introduces turning, milling, planing, grinding, drilling, boring and other common forms of machining accuracy can be achieved.
01 Turning
Workpiece rotation, turning tool in the plane for linear or curved movement of the cutting process.
Turning is generally carried out on the lathe, which processes the internal and external cylindrical surfaces of the workpiece, end face, tapered surface, molding surface, and threads.
Turning machining accuracy is generally IT8 ~ IT7, surface roughness of 1.6 ~ 0.8μm.
(1) In rough turning, the goal is to maintain a high cutting speed. To improve turning efficiency, a large depth of cut and a large feed rate are used.
However, the machining accuracy achieved is limited to IT11. The resulting surface roughness ranges from Rα 20 to 10 μm.
(2) Semi-finish turning and finish turning try to use high-speed and smaller feed and depth of cut, machining accuracy up to IT10 ~ IT7, surface roughness of Rα10 ~ 0.16μm.
(3)On a high-precision lathe, a finely sharpened diamond turning tool can achieve excellent results for high-speed precision turning of non-ferrous metal parts.
The machining accuracy can reach IT7 to IT5. The surface roughness can be as low as Rα 0.04 to 0.01 μm. This type of turning is commonly referred to as “mirror turning.”
02 Milling
Milling refers to the use of rotary multi-flute cutting tools to cut the workpiece, is a high-efficiency machining method.
It is suitable for machining flat surfaces, grooves, various shaped surfaces (such as splines, gears, and threads), and special-shaped surfaces of molds and dies.
According to the milling of the main movement speed direction and the workpiece feed direction of the same or the opposite, and is divided into milling and reverse milling.
The machining accuracy of milling is generally up to IT8~IT7, and the surface roughness is 6.3~1.6μm.
(1) The machining accuracy of rough milling is IT11~IT13, and the surface roughness is 5~20μm.
2) Machining accuracy IT8~IT11 in semi-finish milling, surface roughness 2.5~10μm.
3)Finish milling with machining accuracy IT16~IT8 and surface roughness 0.63~5μm.
03 Planing
Planing is a cutting processing method in which the planing tool makes horizontal relative linear reciprocating motions to the workpiece. It is mainly used for shaping parts.
The machining accuracy of planing is generally up to IT9~IT7, and the surface roughness is Ra6.3~1.6μm.
(1) Rough planing machining accuracy can reach IT12~IT11, surface roughness is 25~12.5μm.
2) Semi-finish planing machining accuracy up to IT10~IT9, surface roughness 6.2~3.2μm.
3)Fine planing machining accuracy can reach IT8~IT7, surface roughness is 3.2~1.6μm.
04 Grinding
Grinding is a machining method that removes excess material from a workpiece using abrasives.
It is considered a finishing process. This method is widely used in the machinery manufacturing industry.
Grinding is usually used for semi-finishing and finishing, the precision can be up to IT8~IT5 or even higher, the surface roughness is generally grinding for 1.25~0.16μm.
(1) The surface roughness of precision grinding is 0.16~0.04μm.
(2) Ultra-precision grinding surface roughness of 0.04 ~ 0.01μm.
(3) The surface roughness of mirror grinding can be up to 0.01μm or less.
05 Drilling
Drilling is a basic method of hole processing, drilling is often carried out on drilling machines and lathes, but also on boring machines or milling machines.
The machining accuracy of drilling is low, generally only up to IT10, the surface roughness is generally 12.5~6.3μm, after drilling is often used to reaming and reaming for semi-finishing and finishing.
06 Boring
Boring is a cutting process used to enlarge a hole or other circular internal contour.
Its application typically ranges from semi-rough machining to finishing. The tool used for boring is usually a single-edged boring tool, commonly known as a boring bar.
(1) The boring accuracy of steel materials is generally up to IT9~IT7, surface roughness of 2.5~0.16μm.
(2) Precision boring accuracy can reach IT7 ~ IT6, surface roughness of 0.63 ~ 0.08μm.
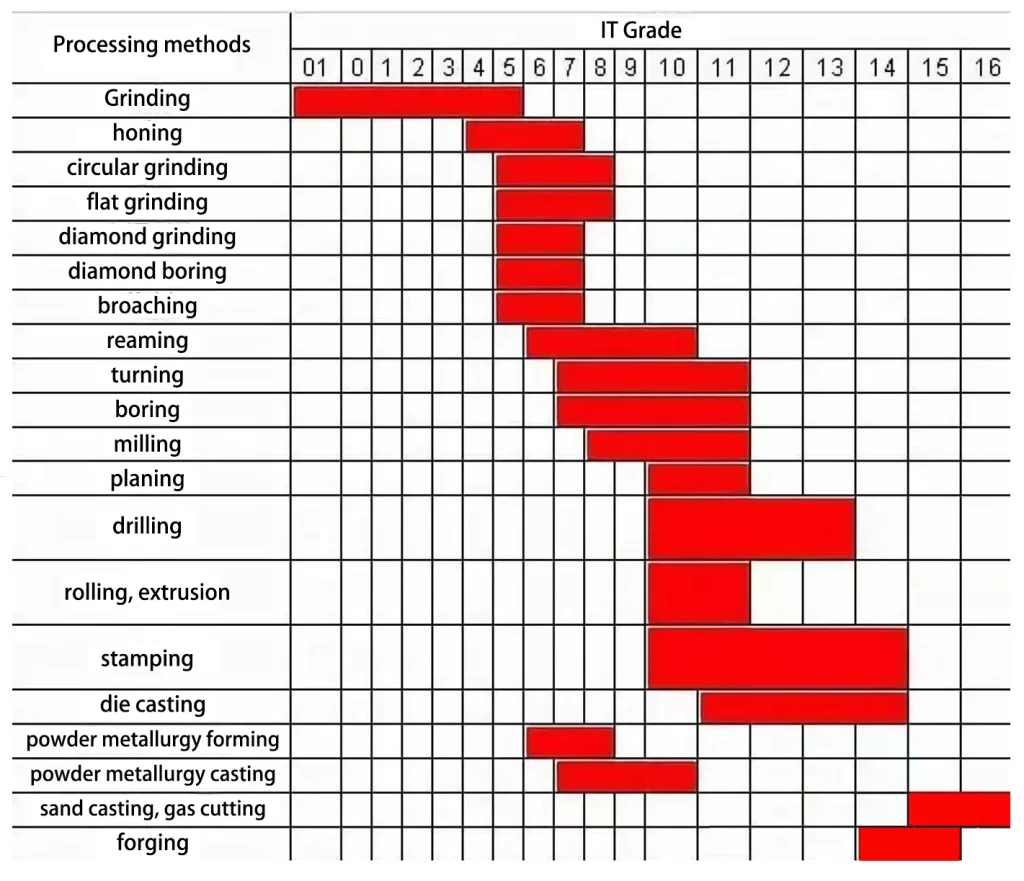
Summarize
With the development of intelligent manufacturing and automation technology, machining accuracy is increasing.
High-precision CNC machine tools are key in advancing the manufacturing industry.
AI-enabled adaptive machining systems are also contributing to this progress.
Additionally, nanomanufacturing technology breakthroughs drive the industry toward greater efficiency and precision.
Are you facing an increased demand for high-precision machining in the manufacturing industry?
How to balance cost and precision is a question that every enterprise needs to consider.