As technology evolves, the manufacturing sector’s focus on CNC machining efficiency and quality positions high-speed cutting as the key to high-performance CNC operations.
Optimize high-speed cutting process, improve equipment performance can not only effectively reduce production costs, but also improve machining accuracy and surface quality.
Although significant progress has been made in the research of high-speed cutting processes, Researchers still face the challenge of boosting efficiency and performance without compromising machining stability.
Studying key factors and optimization in high-speed cutting is vital for advancing manufacturing technology.
Experimental preparation and experimental process
Selection of experimental equipment and cutting tools
This study chooses XYZ-1000 high-precision CNC lathe as the experimental equipment, which has high dynamic response capability and precise positioning control system, and can effectively guarantee the machining accuracy and stability in the high-speed cutting process.
The machine achieves high-speed cutting capabilities for a wide range of complex workpieces by integrating a high-rigidity spindle and a stable drive system.
Researchers added sensors to monitor force and temperature in real time during cutting to ensure accurate measurement of cutting force and temperature during the experiment.
Researchers selected polycrystalline diamond tools for cutting due to their exceptional hardness, wear resistance, and thermal stability. These tools effectively meet the demands of high-speed cutting regarding cutting force, surface quality, and tool life.
Material and size selection of experimental workpiece
Researchers selected 7050 high-strength aluminum alloy as the experimental material due to its excellent mechanical properties, corrosion resistance, and machinability. This alloy is widely utilized in the aerospace and automotive industries.
7050 aluminum alloy, with its high strength and moderate cutting performance, is one of the typical materials in high-speed cutting. Its chemical composition mainly includes aluminum, zinc, copper, and magnesium, and it has high tensile strength and good plasticity.
Researchers used an 80×150 mm cylindrical aluminum alloy workpiece in the experiment.
To investigate the effect of different cutting conditions on machining performance, researchers pretreated the surface of the workpiece, the guarantee is about 2.81 g/cm3, Young’s modulus is 70 Pa, these properties determine its high machining efficiency and low cutting resistance in high-speed cutting.
Experimental parameters and method design
To study the effect of high-speed cutting process parameters on machining performance, the researchers designed a series of experiments to regulate process parameters such as cutting speed, feed and depth of cut, and other process parameters and analyze their effect on machining results.
In the experiments, the cutting speed was set to 400 m/min, 600 m/min, 800 m/min, 1 000 m/min to study the effect of different cutting speeds on the surface quality of the workpiece and cutting force;
The feed was set to 0.1 mm/r, 0.2 mm/r, 0.3 mm/r to analyze the effect of feed change on cutting temperature and machining accuracy;
The depth of cut was set to 1 mm, 2 mm and 3 mm to study the effects on cutting force, surface roughness and tool wear.
The researchers repeated each set of experiments three times to enhance the accuracy and reliability of the experimental data.
The researchers focused on key experimental parameters, including cutting speed, feed rate, and depth of cut.
They analyzed results and used statistics to identify the optimal process parameters.
The experiment also pays special attention to the use of coolant to study its effect on cutting temperature and surface quality. To improve the comparability of the experiments and the accuracy of the data, the researchers conducted all the experiments under a constant ambient temperature to ensure consistency, using the same type and size of tools.
Experimental results
Effect of cutting speed on machining quality
In the high-speed cutting process, cutting speed has a significant effect on machining quality indicators such as surface quality, cutting force, and cutting temperature. The experiment shows that as cutting speed increases, the cutting force shows obvious non-linear changes.
Higher cutting speed leads to an increase in cutting heat, which in turn increases the surface temperature of the workpiece and affects the surface quality. In particular, the surface roughness increases significantly at higher cutting speeds.
Experimental data show that when the cutting speed increases from 400 m/min to 1 000 m/min, the surface roughness increases by about 30%.
Although increasing the cutting speed can improve machining efficiency, too high a cutting speed will lead to the accumulation of cutting heat and the increase of cutting force, which will accelerate tool wear and deteriorate the workpiece’s surface quality. The effect of cutting speed on surface roughness is shown in Table 1.
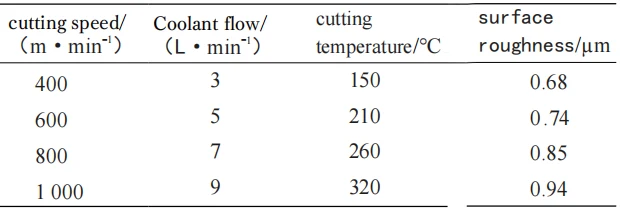
Table 1 shows that with the increase of cutting speed and feed, the surface roughness shows a rising trend. The surface roughness increases from 0.68 µm to 0.94 µm when the cutting speed is increased from 400 m/min to 1,000 m/min.
The data show that higher cutting speeds directly affect surface quality, mainly through increased surface roughness.
Influence of feed on machining quality
Feed rate is one of the critical parameters affecting the machining quality. The experimental results show that the surface roughness increases significantly with the increase of feed. Under the condition of higher feed, the surface roughness is larger, and the cutting temperature also increases significantly.
The experimental data show that surface roughness reaches its maximum value at a feed rate of 0.4 mm/r and is lower at a feed rate of 0.1 mm/r. Table 2 shows the effect of feed on surface roughness and cutting temperature.
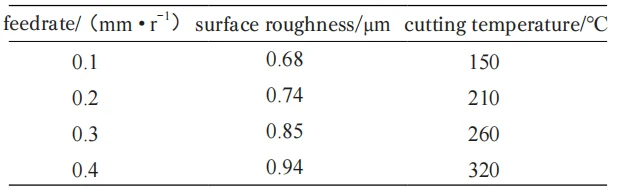
Increasing the feed rate usually leads to a rise in cutting temperature, and the higher cutting temperature can easily lead to the increase of tool wear and the increase of cutting edge fillet, which can significantly shorten the tool life.
At high feed rates, the acceleration of tool wear leads to a decrease in machining accuracy. At the same time, higher cutting speeds may impair surface quality, especially by increasing surface roughness.
Therefore, in the actual machining process, choosing the feed rate reasonably is important to extend the tool life and improve the machining quality.
As shown in Table 2, the surface roughness and cutting temperature show an increasing trend with the increase of feed rate. At a feed rate of 0.4 mm/r, the surface roughness reaches 0.94 µm, and the cutting temperature increases to 320 ℃.
The data show that the higher feed directly leads to the deterioration of surface quality and the increase of cutting temperature, which affects the machining accuracy and tool life.
Effect of depth of cut on machining quality
To systematically analyze the effect of depth of cut on machining quality, Researchers designed the experiment with different depth of cut conditions to observe the change in cutting force, cutting temperature and surface roughness.
The experimental results show that as the depth of the cut increases, the cutting force and cutting temperature increase, while the surface roughness also increases.
This indicates that a larger depth of cut directly leads to an increase in cutting force and cutting temperature, which in turn affects the surface quality of the workpiece.
The results of the data analysis show that when the depth of cut increases, the cutting temperature increases, especially at larger depths of cut, In some cases, the cutting temperature exceeds 250°C, which significantly increases surface roughness and accelerates tool wear.
Therefore, controlling the depth of cut is the key to maintaining machining quality and extending tool life. Table 3 shows the relationship between depth of cut and surface roughness.
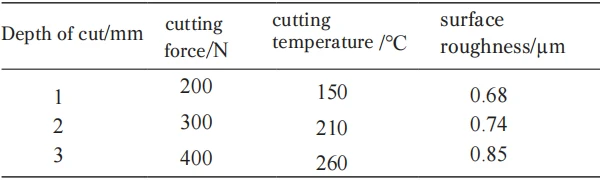
From Table 3, it can be seen that as the depth of cut increases, the cutting force, cutting temperature and surface roughness all show an upward trend.
Increasing the depth of cut from 1 mm to 3 mm caused the surface roughness to rise from 0.68 µm to 0.85 µm, directly leading to the deterioration of surface quality. At larger cut depths, the cut temperature rise significantly affected the machining results.
High-speed cutting process parameters optimization points
Cutting Speed and Its Impact on Machining
High cutting speed can improve machining efficiency. However, too high a cutting speed increases cutting temperature, affecting surface quality, leading to higher tool wear and shorter life.
A reasonable choice of cutting speed is crucial for improving productivity and processing quality. A 600-800 m/min cutting speed range results in relatively stable surface roughness and cutting force, making it suitable for most machining tasks.
Feed Rate and Its Effect on Machining
Higher feed rates increase productivity, but excessive feed rates significantly raise cutting forces and temperatures, which can affect machining stability and surface quality.
At a feed rate of 0.2-0.3 mm/r, cutting forces are relatively low, and surface quality remains good, making this range optimal for efficient machining.
Depth of Cut and Its Impact on Tool Wear
The impact of depth of cut on machining performance is complex. A greater depth of cut increases cutting force, generating more cutting heat, which accelerates tool wear. However, if the depth of cut is too small, the tool’s performance may not be fully utilized, resulting in reduced efficiency.
Process Parameter Optimization
A comprehensive analysis of cutting speed, feed, and depth of cut is essential. Optimizing these parameters can significantly improve processing quality and productivity.
According to experimental data, researchers control the cutting speed at 600-800 m/min, feed at 0.2-0.3 mm/r, and depth of cut at 1-2 mm to achieve better machining results.
Core of Process Parameter Optimization
Process parameter optimization aims to establish a dynamic equilibrium model between cutting force, temperature, and material removal rate.
From an energy dissipation perspective, the matching of cutting speed and feed must meet the optimal energy distribution solution: a high cutting speed can increase material removal rate but may lead to excessive conversion of cutting energy into heat, disrupting the thermal equilibrium at the tool-workpiece interface.
Feed and Shear Angle Considerations
The feed rate should also consider the impact of chip thickness on the shear angle. A feed rate that is too high will increase shear surface stress, inducing cutting vibration.
Optimizing Cutting Depth Using Fracture Mechanics
Optimizing cutting depth with fracture mechanics helps prevent subsurface cracks caused by excessive cutting layer thickness. For example, in the finishing stage, a smaller depth of cut can enhance surface integrity by reducing residual stress gradients and lowering the main cutting force component.
Multi-Parameter Co-Optimization Strategy
This multi-parameter co-optimization is fundamentally a control strategy based on system stability. Researchers need to clarify the coupling mechanism of each parameter through theoretical modeling.
Effect of equipment performance improvement on machining effect
XYZ-1000 CNC lathe adopts double-wall box bed structure,The researchers improved its damping characteristics by 30% compared with the traditional single-wall structure, and they reduced the vibration acceleration measured at 800 m/min cutting speed from 5.2 m/s² to 3.6 m/s².
The spindle unit adopts ceramic hybrid bearings and hydraulic preload technology to increase the axial stiffness to 1,800 N/µm, We control the radial runout to less than 2 µm.
Experimental data show that the spindle’s temperature rise is only 8 ℃ after 4 h of continuous machining, which is 45% lower than that of the traditional steel bearing spindle. This significantly reduces the impact of thermal deformation on machining accuracy and provides a hardware basis for optimizing process parameters.
The XYZ-1000 CNC lathe used in this study has high rigidity and low thermal deformation, which enables the machine to maintain good machining accuracy and low cutting force fluctuations during high-speed cutting.
The high rigidity and high precision servo system of the machine tool can effectively inhibit the vibration generated during the cutting process, reduce the machining error and ensure the dimensional accuracy and surface quality of the workpiece.
The machine tool’s cooling system and temperature control technology play important roles in the high-speed cutting process.
Enhanced automation and intelligence enable real-time parameter adjustment to keep machining optimized.
The intelligent monitoring system of the machine tool can monitor the cutting force, temperature, vibration and other key parameters in real time, and adjust the processing parameters according to the feedback of the data to avoid overload, overheating and other undesirable situations, and then optimize the processing effect.
Conclusion
The researchers analyzed and experimentally verified high-speed cutting process parameters and equipment performance.
The experimental results show that a reasonable choice of cutting speed, feed and depth of cut can effectively improve machining quality, reduce cutting force and temperature, and improve surface roughness.
Cutting tool wear is closely related to cutting force and temperature, optimizing cutting process can extend tool life and improve machining efficiency.
Enhancing the performance of the equipment can guarantee the machining accuracy and cutting stability, thus providing a theoretical basis and practical guidance for further improving the comprehensive performance of high-speed cutting and machining, This contributes greatly to the technological progress in related fields.