The birth of five-axis CNC machine tools, in the digital processing technology in the core processing position, greatly improving the processing efficiency and reduce processing costs.
The so-called digital processing refers to the use of CAD, CAM, CNC, PLC, and other digital technologies.
In digital processing, the design drawings that need to be processed are converted into process documentation.
This documentation is then transformed into a command code that the machine tool can recognize and execute.
As a result, the machine automatically completes the processing operation according to the processing technology.
And digital processing technology has become an important symbol of the manufacturing industry.
In the early manufacturing industry, parts design drawings were processed using ordinary lathes, milling machines, drilling machines, grinders, and other single traditional machine tools.
This processing method was relatively simple. However, it had low machining accuracy and positioning accuracy. Additionally, the process was complex.
With the development of science and technology, CNC lathes, milling machines, turning centers, and five-axis processing machine tools have been introduced.
These advancements have made the processing of parts more centralized. As a result, machining accuracy and positioning accuracy have been significantly improved.
The following will be from 4 aspects to talk about the core competitiveness of five-axis linkage CNC machine tools.
Reflect the core competitiveness from the characteristics of five-axis linkage CNC machine tools
The five axes of a five-axis CNC machine tool refer to the X-axis, Y-axis, Z-axis, and two other rotary axes.
According to ISO regulations, a right-handed right-angle coordinate system is used to describe the motion of a CNC machine tool.
The coordinate axis parallel to the main axis is defined as the Z-axis, and the rotary coordinates around the X, Y and Z axes are A, B and C respectively.
The motion of each axis can be realized by the table or by the movement of the tool, but the direction of the tool’s movement relative to the workpiece defines the direction.
Usually, five-axis linkage refers to the linear interpolation motion of any five coordinates in X, Y, Z, A, B, C. The five-axis machine is shown in Figure 1. A five-axis machine is shown in Figure 1.
With a 5-axis CNC machine, it is possible to control three translational degrees of freedom and three rotational degrees of freedom of a rigid body in space.
Using three translational coordinates and two rotational coordinates, the position and attitude of the tool relative to the workpiece can be represented.
Take the Huazhong 848 five-axis CNC system as an example. Its five axes are the X, Y, Z, A, and C axes.
Through the X, Y, and Z orthogonal axes, the tool’s position in space can be determined. The A and C rotary axes allow for the determination of any tilt angle of the tool axis.
All five coordinate axes can be controlled by positioning the parts and adjusting the tool’s attitude.
The definition of the five-axis CNC machine tool clearly states that it can replace most other CNC machine tools.
They are capable of completing the processing of the entire part. Additionally, five-axis CNC machine tools offer more versatility and flexibility.
Five-axis linkage machine tools can process more complex and higher-precision products based on its characteristics.
These machine tools are widely used in aerospace, medical, and military fields. They are handy in parts manufacturing and other areas with a wide range of applications.
As we all know, ordinary CNC milling machines, three-axis machining centers, and four-axis machining centers require multiple clamping operations to process complex parts.
Typically, these machines need to flip the part several times, reposition it, and then complete the processing.
Each additional clamping operation reduces the accuracy of the clamping, decreasing the overall accuracy of the part.
And multiple clamping will also increase the risk of product scratches and bruises, the product scrap rate is naturally high. For enterprises, multiple processes undoubtedly increase the number of machine tools and labor costs.
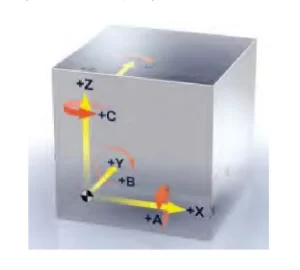
Competitiveness of 5-axis CNC machine tools from a variety of machine types
Users can choose from various types of CNC machine tools based on their needs. Five-axis CNC machine tools are available in three main types, as shown in Figure 2.
These types include the double pendulum table structure, the double rotary table structure, and the pendulum head rotary table structure.
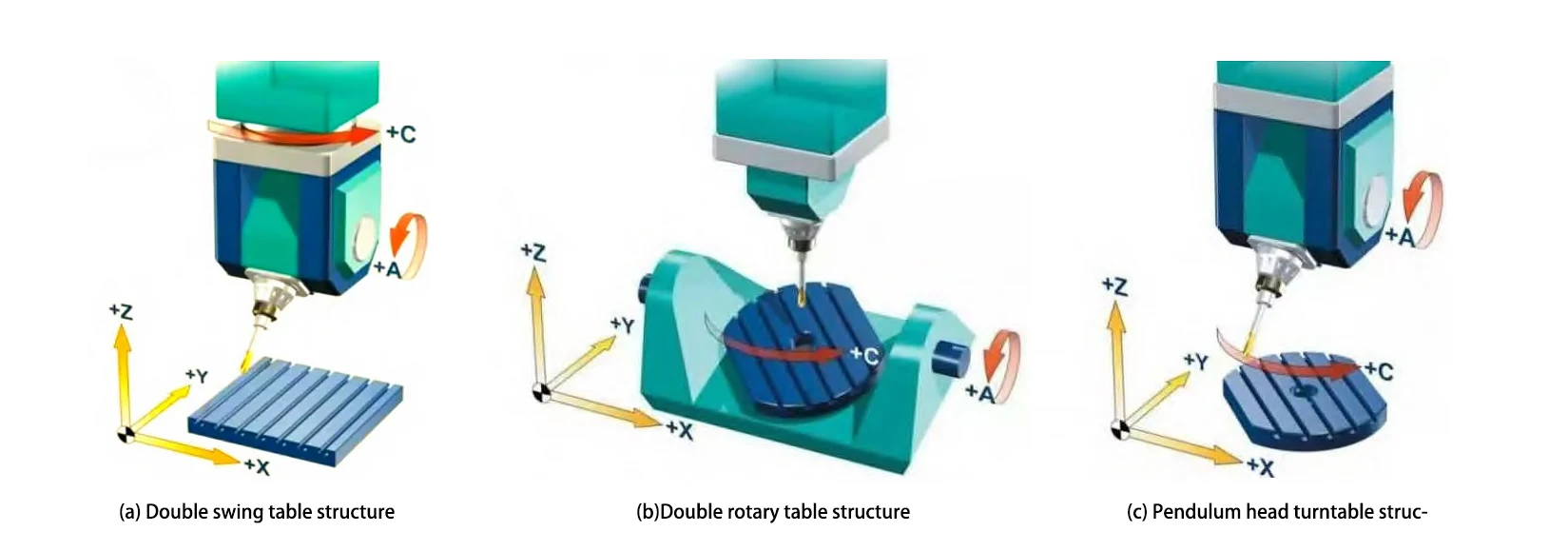
(1) Double pendulum table structure 5-axis CNC machine tool.
The double pendulum structure of five-axis CNC machine tools refers to the two rotary axes on the machining center, generally the A and C rotary axes.
The double pendulum structure provides the machine tool with a greater degree of freedom, enabling the machining of more complex parts.
At the same time, it allows the machine tool to maintain a more stable position and angle during machining.
This reduces the number of repeated clamping operations, improving the parts’ machining accuracy.
Its flexibility allows it to be used in different types of workpiece processing, such as complex curved surfaces, inclined holes, and other machining features.
This greatly improves the machining center’s applicability and scope of application, as well as the machining efficiency and surface finish of the parts.
Its disadvantages are high initial cost, programming difficulty, and high programming skill requirements for programmers.
2) Dual-table structure 5-axis CNC machine.
A five-axis CNC machine with a double-rotary table configuration typically consists of three linear coordinates and two rotary coordinates.
It is capable of performing machining operations with simultaneous coordinated movement. This is achieved under the control of the CNC system.
It is specialized in machining complex surfaces, such as propellers on ships, rotors of heavy electric motors, turbine rotors on automobiles and crankshafts on diesel engines, etc.
This type of CNC machine has better machining results.
Its advantage is that it can achieve complex spatial curvature machining.
This improves the machining accuracy of the parts. Additionally, it reduces the auxiliary time required before machining.
At the same time, the operators’ operational technology requirements are lower compared to double pendulum structure five-axis linkage CNC machine tools.
Moreover, the production requirements for post-processing using CAM software are relatively simple.
Its disadvantage is that it has certain requirements on the design range of the working table, which is not too large and has small load-bearing capacity.
When the A-axis rotation is greater than or equal to 90°, the table is required to have a large load-bearing moment when the workpiece is cut.
Due to the table’s limited design range and the large rotational degree of the A-axis, the table requires a large load-bearing moment.
Additionally, other factors contribute to limiting the machine tool’s capabilities. As a result, the scope of the machine tool and its machining capacity are restricted to a certain extent.
(3) Pendulum head rotary table structure five-axis linkage CNC machine tools.
Five-axis CNC machine tools with a pendulum head and rotary table structure offer more flexibility.
Users have more options between the pendulum head type and the rotary table type.
These options provide greater flexibility regarding product processing range, table travel, and programming requirements.
As a result, programming staff and operators have more choices to meet different machining needs.
Its two rotary axes are placed on the spindle and the table. If the table is used to rotate, larger workpieces can be clamped;
If spindle swing is used, the tool axis can change more flexibly. The spindle structure is also relatively simple and offers better rigidity.
Additionally, the manufacturing cost is lower. However, its load-bearing capacity is limited, so the table cannot be designed too large.
From the advantages of five-axis CNC machine tools to reflect its competitiveness
(1) Reduce the number of clamps.
Compared with the traditional three-axis CNC machine tools, it greatly reduces the number of clamping times and improves the clamping accuracy.
There are a number of different angles of surfaces, especially oblique surfaces, especially in the part design drawings. Complex surface parts are shown in Figure 3.
Especially in the mold products, often need to process the slanting top, slider, electrode and other products, processing surface, processing process is complex, processing features.
Three-axis CNC machine tools typically require multiple clamping operations to meet machining demands. In contrast, five-axis CNC machine tools can complete the process with just a single clamping operation.
This greatly reduces the number of clamping steps and lowers labor costs. At the same time, it helps improve the product qualification rate.
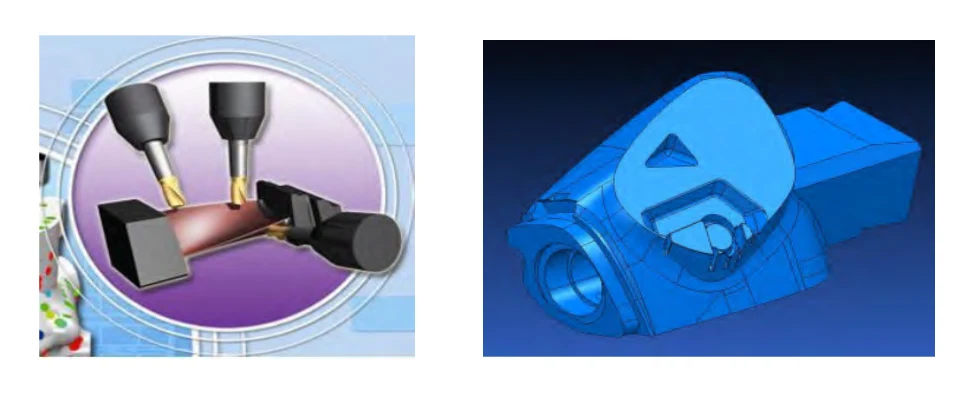
(2) can always maintain the best cutting condition of the tool, improve the cutting conditions.
As shown in Figure 4, the left image illustrates the cutting mode of three-axis CNC machine tools.
The machining schematic shows that as the cutting tool gradually moves toward the top edge of the workpiece, the cutting conditions begin to deteriorate.
This leads to a continuous decline in the surface quality of the part.
As a result, the machining accuracy becomes poor. In addition, the machining time is extended, and overall efficiency remains low.
As can be seen from the figure on the right, if the part needs to maintain the best cutting state of the tool, the table must be rotated.
Similarly, if you need to complete the machining of an irregular plane, the table needs to be rotated several times in different directions.
This type of rotation, five-axis CNC machine tools can be completely realized.
It can also effectively avoid the ball milling cutter center point linear speed of 0 to obtain better surface quality and machining accuracy.
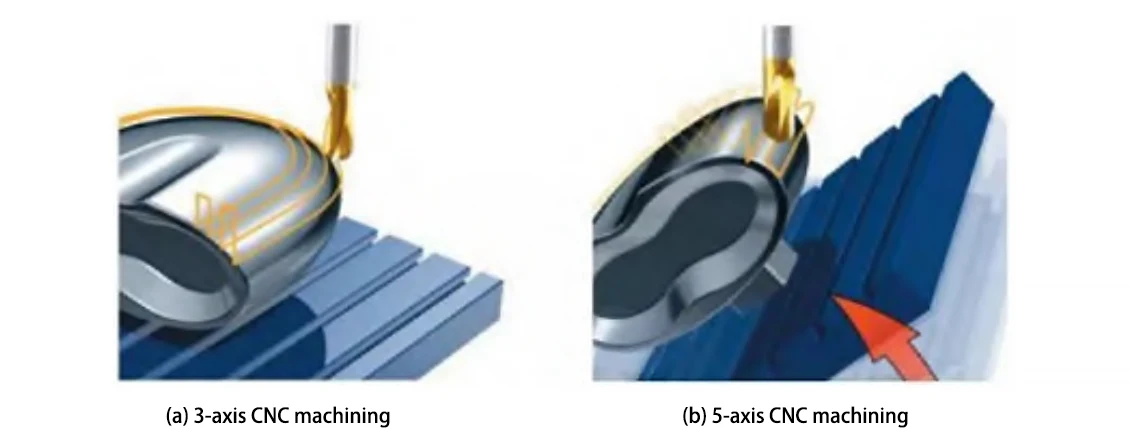
3) Effectively avoid tool interference.
As shown in Figure 5, components such as impellers, blades, and integrally bladed rotors (whole leaf disks) often have complex curved surfaces and bending features.
Three-axis CNC machine tools are unable to complete the machining of these parts. This is mainly due to tool interference and the inability to meet specific process requirements.
At this point, the five-axis machine tool will play out its unique machining advantages.
The use of five-axis machine tools allows for the use of shorter processing tools.
This improves the overall rigidity of the machining system. It also reduces the number of tools required for the process.
This helps avoid the need for special tools to some extent. As a result, processing costs are reduced, and machining efficiency is improved.
(4) The effective combination of five-axis machining and high-speed machining shortens the manufacturing cycle of the mold.
Mold parts processing is shown in Figure 6.
In the traditional machining process, multiple methods are required to complete the entire part. These include the use of a three-axis machining center, EDM, electrode machining, and other techniques.
The overall processing workflow is complex and demands a high skill level from the operators. As a result, the manufacturing cycle for parts is long, and the production costs are high.
However, through five-axis machine tool processing, we can gradually say goodbye to electrical discharge machining and, to a certain extent, change the mold parts and manufacturing process.
This greatly shortens the manufacturing cycle of the mold, which results in cost savings. It also reduces the use of manpower and material resources and greatly improves processing efficiency.
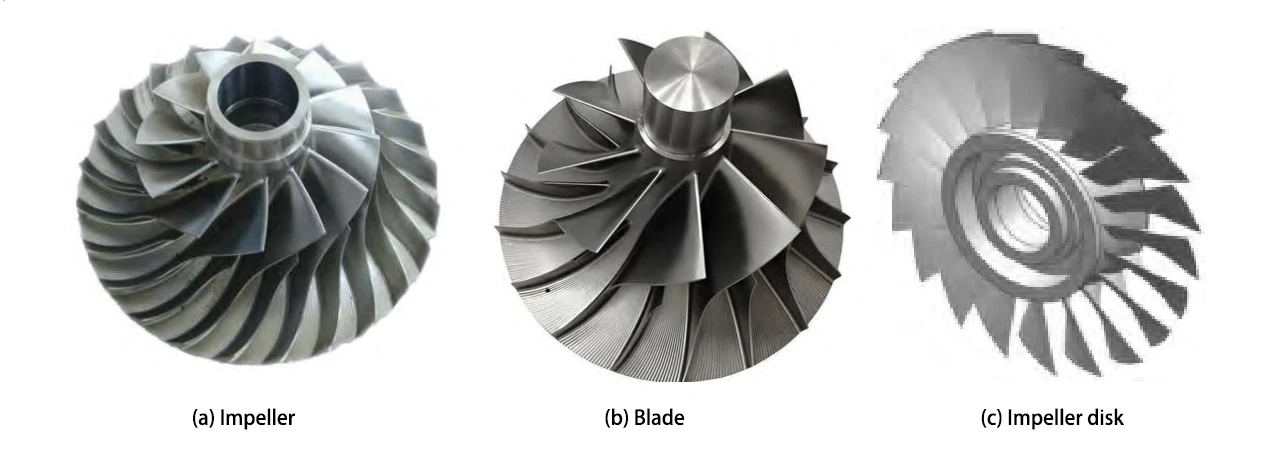
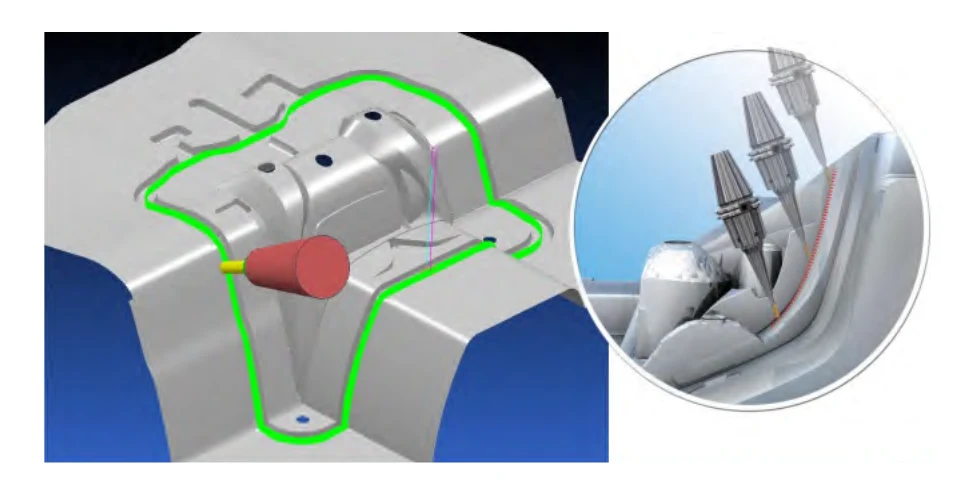
From the five-axis linkage machine tool core technology reflects its competitiveness
(1) Coordinate system transformation technology.
Coordinate system transformation is shown in Figure 7.
Parts can be machinized by changing the coordinate system in the five-axis linkage CNC machine tool.
(2) RTCP function.
RTCP, short for Rotated Tool CenterPoint, is the tool tip point following function, as shown in Figure 8.
In the five-axis machining process, there is a continuous pursuit of the tool tip point trajectory and the relative attitude between the tool and the workpiece.
Due to the rotary movement involved, this process will result in an additional or “attachment” movement of the tool tip point.
In CNC machining, the control points often do not coincide with the actual tool tip point.
To address this, the CNC system automatically corrects the control point.
This correction ensures that the tool tip point follows the established trajectory accurately.
Some professionals in the industry refer to this technology as the TCPM or TCPC function.
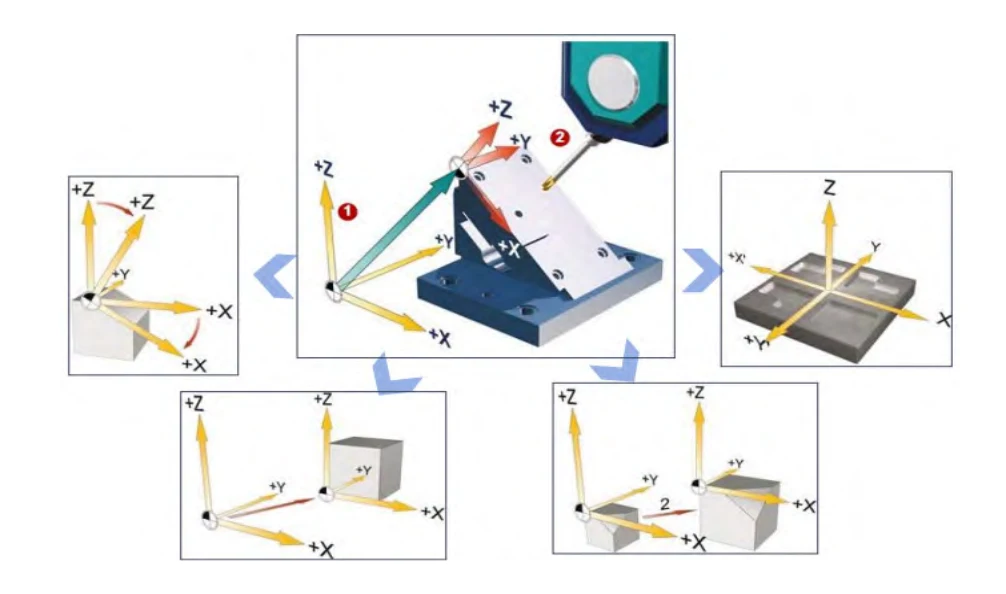
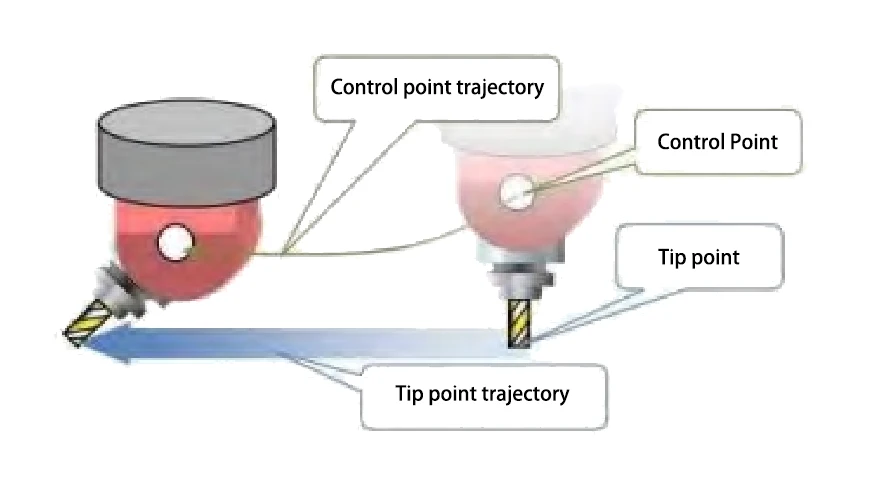
3) Tool axis direction smoothing function.
Turning on the direction smoothing function can not only effectively improve the quality of the machined surface, but also greatly improve the machining efficiency of the parts.
Conclusion
With today’s growing demand for digital machining, the demand for five-axis linked CNC machine tools has also shown a significant upward trend.
With their series of core competitive advantages, five-axis linkage CNC machine tools are gradually increasing their market share.
This trend is expected to continue under suitable application scenarios and with a solid development foundation.
In the future, enterprises and educational institutions will increasingly recognize and adopt these machines.
Practical research shows that five-axis linked CNC machine tools have core competitiveness in digital processing.