Multi-axis CNC machining technology uses a computer system to control multiple CNC axes simultaneously to process multiple tools or parts, effectively improving machining efficiency and quality.
It has a high degree of precision, can use multiple axes on a machine tool for digital control, and complete the processing of complex workpiece operations.
With the development of the automobile industry, the precision requirements for parts processing continue to improve.
As a result, traditional CNC machining technology can no longer meet the demand.
Increasing the degree of freedom of the machine tool can realize more complex machining operations.
Automotive engine crankshafts usually have complex curved surfaces and irregular shapes.
Multi-axis CNC machining technology can handle complex surfaces and improve machining efficiency.
This paper will discuss the application of multi-axis CNC machining technology in automotive engine crankshaft processing.
Multi-axis CNC machining technology principle
Multi-axis CNC machining technology allows the workpiece to complete multiple processes in clamping.
This avoids the positioning errors caused by multiple installations, improving machining accuracy and productivity.
The principle lies in the linkage control of several independent axes, as shown in Figure 1, including three linear axes (X, Y, Z) and two rotary axes (A, B or C).
These axes work together to make the machine tool capable of machining the workpiece in all directions in three-dimensional space.
Specifically:
(1) X, Y, Z axes:
Control the movement of the workpiece in the forward and backward directions, the left and right directions, and the up and down directions.
This ensures the accurate positioning of the workpiece in both the plane and three-dimensional space.
(2) A, B, or C axis:
Control the workpiece’s rotation. The A axis rotates around the X axis, and the C axis rotates around the Z axis (the B axis rotates around the Y axis) to realize rotary processing in different directions.
Advantages of application in automotive engine crankshaft machining
With the continuous development of information technology, CNC technology has become widely used in automotive parts processing.
It can effectively optimize the processing process of automotive parts, improving both processing accuracy and production efficiency.
The advantages of multi-axis CNC machining technology in automotive engine crankshaft applications include the following aspects.
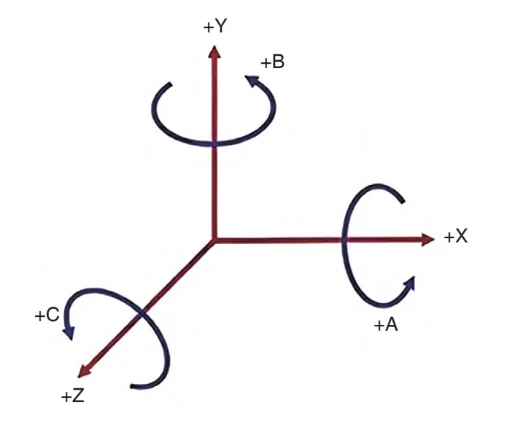
Improve machining accuracy
CNC multi-axis machining centers, such as five-axis, operate with three linear axes: X, Y, and Z.
In addition, rotary axes (such as the A-axis and C-axis) process the workpiece at different angles.
This multi-angle machining capability greatly improves the crankshaft’s machining accuracy and ensures its assembly accuracy and overall performance.
Enhancement of machining efficiency
Multi-axis CNC machining allows multiple faces of the crankshaft to be completed in a single setup.
This significantly improves machining efficiency and helps reduce production costs.
For the automobile manufacturing industry, this means shorter production cycle and higher production capacity, which helps to improve market competitiveness.
Reduce scrap rate
The high precision and stability of multi-axis CNC machining reduce the scrap rate of crankshafts during the machining process.
This can reduce material waste and repeat processing costs, and further improve production efficiency.
Responding to the demand of complex shape machining
As a key engine component, the Crankshaft has a complex shape and variable curvature.
CNC multi-axis machining centers have excellent machining capabilities.
They can easily handle the challenges posed by complex shapes.
This allows them to meet the automotive industry’s demand for high-precision, high-strength crankshafts.
Multi-axis CNC machining key technology analysis
Product structures are becoming more complex. At the same time, the demand for high-efficiency and precision machining continues to grow.
As a result, multi-axis CNC machining technology has become increasingly important.
It has now become an indispensable part of modern machinery manufacturing.
Multi-axis CNC machining key technologies mainly include the following aspects.
A Computer Numerical Control (CNC) system is a program-controlled automated machine tool that belongs to a special real-time multi-tasking computer system.
It uses digital text and symbols with digital instructions to control the machine action and achieve accurate machining operations.
The CNC system is the core of multi-axis CNC technology.
It is responsible for receiving and analyzing programming instructions and controlling the machine’s trajectory and the entire machining process.
The system can ensure the synchronization and coordination of the independent movements of each axis to complete the machining of complex surfaces and irregular shapes.
CNC programming and simulation technology
CNC programming technology
CNC programming refers to the machining process of parts, along with process parameters, machine movements, tool displacement, and other related information.
All of this information is recorded in CNC language within the program list and is verified throughout the machining process.
Primary methods of CNC programming include:
(1) Manual programming: The various stages of programming are manually completed, and the program is short and suitable for simple shapes.
(2) Automatic programming: using computer software that applies to complex parts and long programs can improve programming efficiency and accuracy.
(3) CAD/CAM software: Designers use CAD software for workpiece design and drawing, while CAM software generates CNC programming code.
CNC programming simulation technology
CNC programming simulation is an efficient method of verifying and optimizing CNC programming.
It involves using software tools to simulate the work process of CNC machine tools.
Simulation technology can check and adjust the programming code without requiring real processing.
This helps reduce or even eliminate errors and problems during actual machining.
Commonly used CNC programming simulation software includes VERICUT, Keller CNC simulation software, and others.
Due to space constraints, only a brief description of the VERICUT software is provided below.
VERICUT software can simulate various CNC systems, support for tool position files and CAD/CAM post-processing NC program simulation.
Its ability to optimize NC programs, reduce machining time, extend tool life, improve surface quality, and prevent machine collisions and over-travel errors characterizes it.
This software’s simulation process mainly includes several key steps.
These include establishing the machine model, defining motion relations, and calling the controller for simulation.
Other related steps are also involved, as shown in Table 1.
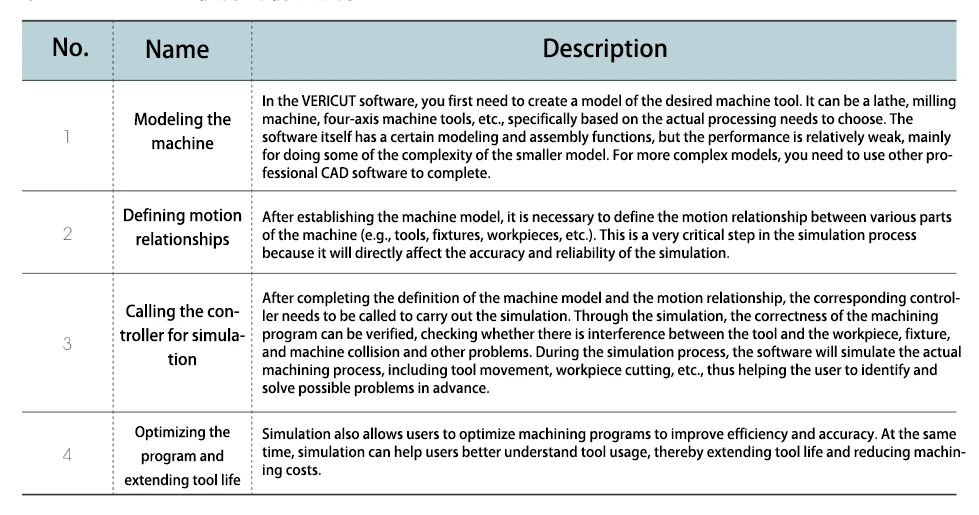
Cutting process
The cutting process involves tool selection, cutting parameter setting, and cutting process control. It significantly impacts machining efficiency and quality.
The key factors are the three elements of cutting: cutting speed, feed, and depth of cut.
Intelligent control technology
Intelligent control technology uses artificial intelligence and machine learning to optimize and adaptively adjust the machining process intelligently.
This further improves machining efficiency, reduces machining costs, and enhances the quality of parts processing.
In the automotive engine crankshaft processing in the application process
Equipment debugging and program writing
In the beginning of the actual processing before the need for multi-axis CNC machine tools for debugging, to ensure that the normal operation of the equipment and processing programs.
Determine the origin of the workpiece coordinate system, and write the CNC program through CAD/CAM software, and then input it into the machine controller.
CAD/CAM software, through the preparation of CNC program methods and steps, mainly includes the following aspects, as shown in Table 2.
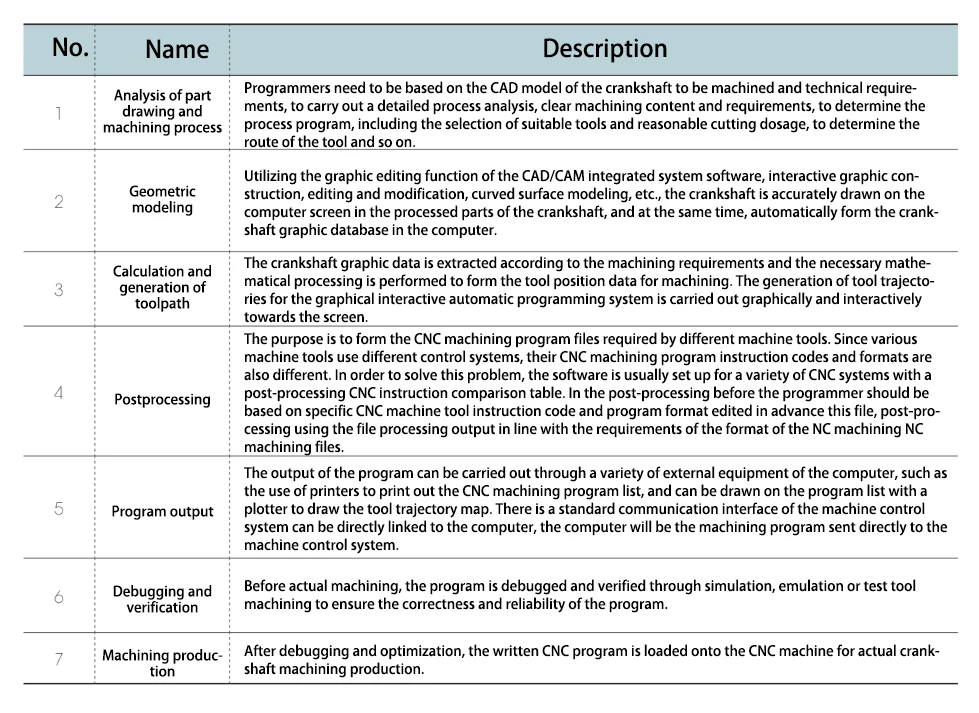
CAD / CAM software can significantly improve programming efficiency, reduce manual errors, and simplify automotive engine crankshaft CNC programming.
However, the programmer still needs to analyze the crankshaft drawing carefully and perform the necessary mathematical processing.
Figure 2 shows the position and role of the CNC program in the multi-axis CNC machining system.
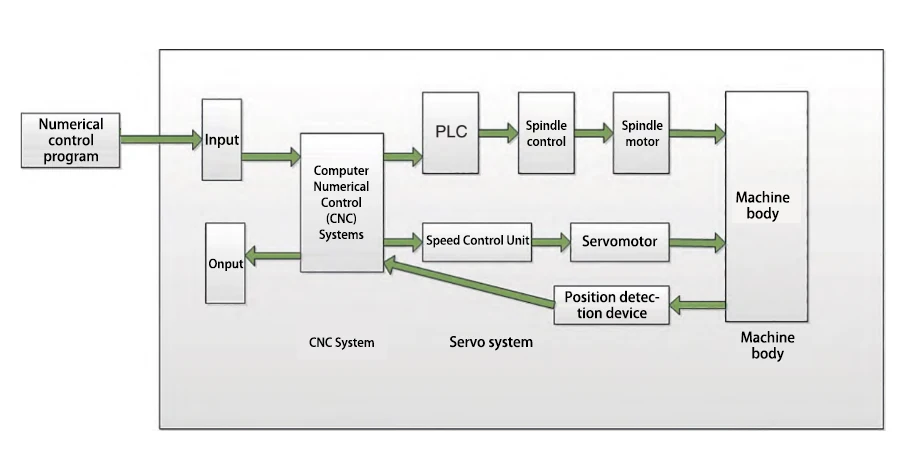
Clamping workpiece
Fix the crankshaft workpiece on the fixture. Measure the relative position of the workpiece coordinate system according to the part design requirements.
Then, input the position coordinate value into the machine controller to determine the absolute coordinate system point of the workpiece. Fill in the machining parameters to prepare for subsequent machining.
Roughing
According to the program, the crankshaft is roughly machined by a multi-axis CNC machine, removing a large amount of residual material to make the overall shape of the crankshaft take shape.
In the rough machining process, the main concerns are the machining efficiency and the overall shape of the workpiece, which should lay a good foundation for the subsequent machining.
Semi-finishing
Based on rough machining, semi-finishing is carried out to improve the crankshaft machining accuracy further.
Semi-finishing usually uses smaller diameter ball-end milling cutters to remove the excess, providing a more perfect surface for the final finishing.
Finishing
Finishing is the most critical step in multi-axis CNC machining technology, and it is necessary to improve the crankshaft accuracy to the highest level.
A fine groove milling cutter is used for cutting. The cutting depth is very small to ensure the crankshaft’s surface quality and dimensional accuracy.
In the finishing process, the crankshaft is inspected for various aspects, such as size, deviation, and surface quality, to ensure that it meets the design requirements.
Conclusion
The application of multi-axis CNC machining technology in automobile engine crankshaft machining has significant advantages.
It can improve machining accuracy and efficiency, reduce production cost and scrap rate, and ensure the high precision and quality of crankshafts, meeting the high requirements of automobile engine crankshafts.
The key technologies include CNC systems, CNC programming and simulation technology, cutting processes, intelligent control technology, and more.
This technology’s application process in automobile engine crankshaft machining includes equipment debugging and program writing, workpiece clamping, roughing, semi-finishing, and finishing.
It is believed that in the future, with the continuous development of multi-axis CNC machining technology, it will promote the high precision, high efficiency and high quality of automobile engine crankshaft machining.