With the rapid development of the modern manufacturing industry, CNC machining technology has become widely used in metal material processing.
CNC machining has the advantages of high precision, high efficiency, and a high degree of automation, and it can meet the processing requirements of complex parts.
However, during CNC machining, residual stress will be generated within the metal material due to the cutting force, cutting heat, and other factors.
Residual stresses will adversely affect the dimensional accuracy, shape accuracy, fatigue strength, and other properties of the parts and even lead to deformation and cracking.
Therefore, studying the distribution and elimination methods of residual stress in the CNC machining of metal materials is of great practical significance.
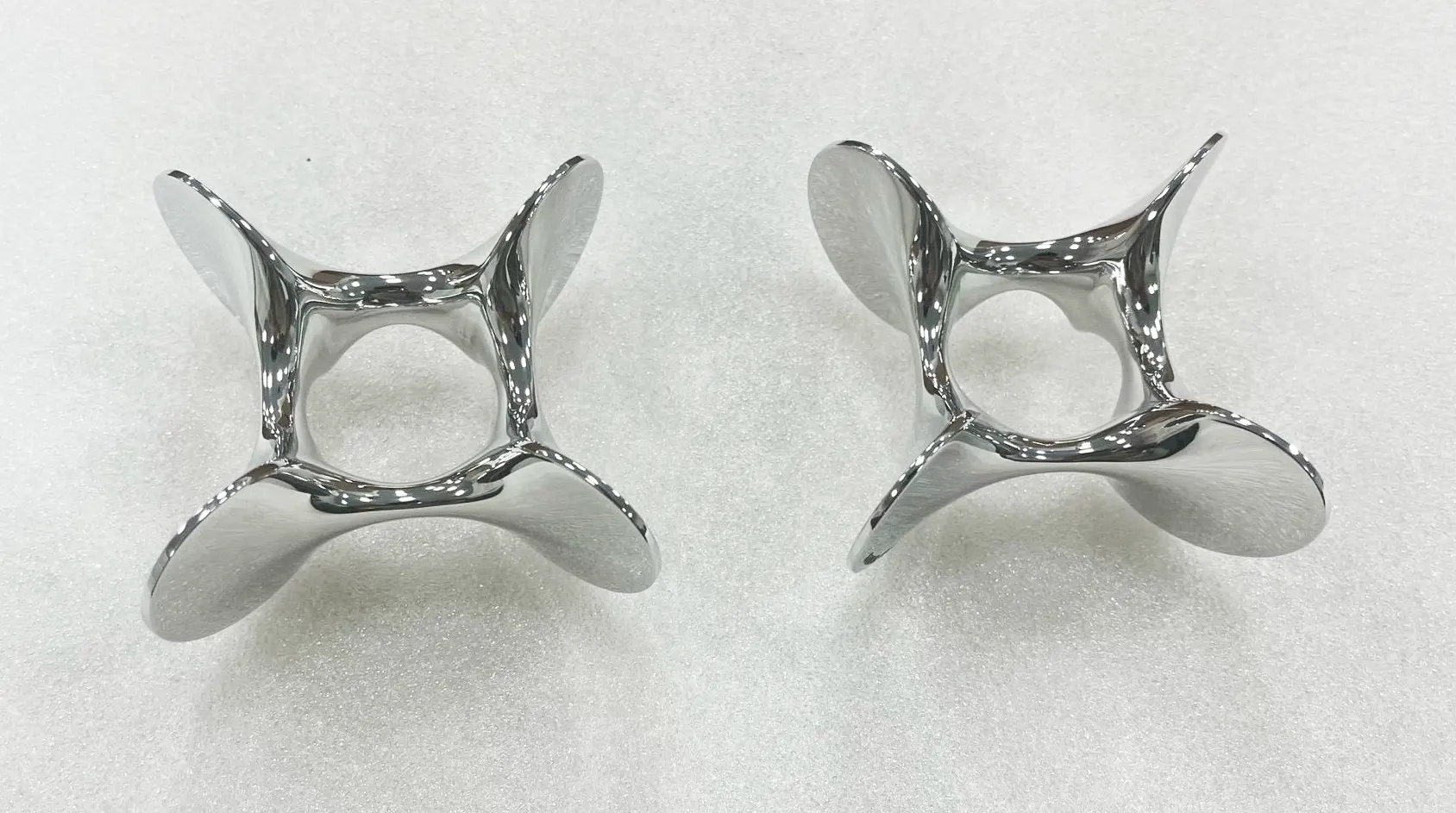
Mechanism of residual stress in the CNC machining process
1. Residual stress caused by cutting force
Due to the role of the cutting force in CNC machining, metal materials experience complex deformation.
The cutting force will not only cause elastic deformation of the metal material but also cause plastic deformation.
When the cutting force is removed, the elastically deformed part of the material naturally returns to its original state, while the plastic deformation remains permanently, which leads to residual stresses.
Typically, the size of the cutting force is directly proportional to the degree of plastic deformation, so the higher the cutting force, the more severe the plastic deformation, and accordingly, the residual stresses will also increase.
2. Residual stress caused by cutting heat
In CNC machining, the cutting process inevitably generates heat.
As the tool removes the metal material in a high-speed rotation, the friction and plastic deformation release a large amount of heat energy, resulting in a rise in material temperature.
As the temperature rises, the material undergoes thermal expansion, i.e., an increase in its volume or size.
However, after the heat generated by cutting is removed, although the material’s temperature begins to decrease, the volume or size change due to the previous thermal expansion does not fully return to the initial state, resulting in the formation of so-called residual stresses.
Residual stress is the stress that exists inside the material without the action of an external force.
The heat level of cutting directly affects the degree of thermal expansion; therefore, the higher the heat of cutting, the greater the thermal expansion and, ultimately, the more significant the residual stresses.
The existence of residual stresses will impact the material properties and machining accuracy; therefore, measures need to be taken to control the generation and distribution of cutting heat in CNC machining.
3. Residual stress caused by phase change
In the field of CNC machining, in addition to the phenomenon of thermal expansion of the material caused by the cutting heat, this heat may also lead to phase changes within the metal.
The so-called phase change refers to the process in which a substance is transformed from one crystalline structure to another, and a volume change often accompanies this process.
When steel, for example, is hardened, it transforms from austenite to martensite, leading to an increase in volume and, consequently, to residual stresses.
The volume change accompanying the phase transformation process is one of the key factors causing residual stresses.
The presence of residual stresses can significantly change the material’s physical properties, such as hardness and toughness, and in serious cases, may even cause distortion of the workpiece’s shape or the formation of cracks.
In view of this, reasonable control of the temperature rise in the cutting process and its distribution, as well as effective cooling and lubrication measures, are essential in practice to reduce the residual stress caused by phase change.
CNC machining parameters affecting residual stresses
1. Cutting speed
Cutting speed is a key parameter in CNC machining, and its influence mechanism on residual stress is very complex. Generally speaking, increasing the cutting speed will increase the temperature of the cutting area.
This increase in temperature triggers thermal softening of the material, which reduces the degree of plastic deformation.
As a result of this reduction in plastic deformation, residual stresses typically decrease.
However, when the cutting speed exceeds a specific threshold, the cutting forces increase significantly, which in turn increases the plastic deformation and leads to an increase in the residual stresses.
While increasing cutting speeds can improve machining efficiency to some extent, it also poses the challenge of effectively controlling temperature and coping with changes in material properties.
Therefore, engineers must carefully select the right cutting speed in practice to ensure that they can meet productivity demands while effectively managing residual stresses and preventing unacceptable deformation or damage to the workpiece.
2. Feed
As one of the key machining parameters, the feed’s value directly impacts the cutting forces.
As the feed increases, the resistance encountered during the cutting process increases, intensifying the degree of plastic deformation of the material and leading to an increase in the level of residual stress.
In addition, the increased feed rate promotes the generation of more heat in the cutting zone, which, on the one hand, causes the material to expand due to the increased temperature and, on the other hand, may further increase the temperature in the zone.
Both of these factors increase the residual stresses in the final workpiece.
Precise feed rate control is essential for optimizing productivity and ensuring product quality.
If the feed rate is set too high, it can accelerate the rate of material removal, but it can also accelerate tool wear and reduce its useful life;
On the other hand, if the feed rate is set too low, it will help extend the tool life cycle, but it will also reduce work efficiency and indirectly increase the manufacturing cost.
Therefore, in practice, it must be based on specific working conditions and target requirements, with flexible adjustment of feed parameters, to achieve the best processing results.
3. Cutting depth
In metal cutting, the depth of the cut is a critical parameter, directly affecting the strength of the cutting force and the heat generated during the cutting process.
If a more significant depth of cut is selected, it will result in a substantial increase in cutting force, accompanied by a large amount of heat generation.
This increase in force and temperature will induce the machined material to undergo more pronounced plastic deformation and exacerbate the phenomenon of thermal expansion.
Ultimately, these physical changes result in elevated levels of residual stresses within the finished product.
In view of this, in the field of CNC machining technology, the scientific and reasonable setting of the depth of the cut is particularly critical because it can not only effectively regulate the degree of residual stress within the final product but also directly determine the accuracy and overall quality of parts processing.
CNC machining residual stress distribution law
1. Distribution along the cutting depth direction
In the CNC machining of metal materials, along the cutting depth direction, observed residual stress presents a specific distribution pattern.
Specifically, the material’s surface is usually in a state of compressive stress, while its internal tensile stress state.
This phenomenon is mainly attributed to the material’s plastic deformation and thermal expansion due to the forces exerted by the tool and the heat generated during the cutting process.
As the thermal expansion of the surface layer of the material is limited by the surrounding material, compressive stresses are formed during cooling;
In contrast, the inner material is less affected by external forces, and during the contraction of the surface material, the inner material is subjected to tensile stresses.
This stress distribution has important implications for the properties of metallic materials and their structural integrity.
For example, appropriate surface compressive stresses can help enhance the material’s ability to resist fatigue and corrosion, but internal tensile stresses may trigger cracks or even fractures.
Therefore, mastering and controlling this stress distribution characteristic is crucial for improving the quality and efficiency of CNC machining.
2. Distribution along the feed direction
In the feed direction, the distribution of residual stress presents more complex characteristics.
This distribution is affected by a variety of factors, such as cutting parameters, geometry, material properties, cooling conditions, and the processing environment.
Typically, the residual stresses are higher near the cutting edge due to the higher cutting forces and thermal effects and the significant plastic deformation caused by the tool’s direct action on the material.
As the distance from the cutting edge increases, the residual stress decreases, mainly because the area away from the cutting edge is subjected to weaker cutting influences.
The intensity of the thermal and mechanical effects decreases, thus reducing the degree of plastic deformation.
It can be seen that in the execution of cutting operations, a reasonable choice of cutting parameters and tool geometry and optimization of cooling and lubrication measures play important roles in effectively controlling and improving the distribution of residual stress on the surface of the workpiece.
3. Distribution along the part surface
On the part’s surface, residual stresses distribution shows significant non-uniform characteristics.
Specifically, the residual stress value is usually higher in the path of the cutting edge because the region is subjected to more concentrated mechanical forces and thermal effects.
These concentrated effects lead to significant changes in the stress state in the material’s internal structure.
In contrast, other parts of the material that are not directly affected by the cutting edge experience weaker external forces and thermal effects, so the residual stress level is relatively low, and the internal stress condition of the material is more stable and does not exhibit significant stress concentration.
Experiments on residual stresses in CNC machining of metal materials
1. Experimental Methods
Two experimental methods, X-ray diffraction and blind hole, were used to accurately measure the residual stresses generated after CNC machining of metal materials.
Through the designed experimental program, the cutting parameters were systematically adjusted, including but not limited to cutting speed, feed, and depth of cut and other key factors.
By changing these parameters, it aims to deeply study and reveal the change rule of residual stress and the potential influence on the material properties.
2. Experimental results and analysis
The detailed study of the experimental data shows that the effect of cutting parameters on the residual stress within the metal material after CNC machining is very significant.
In particular, as the cutting speed increased, the residual stresses first decreased and then increased, whereas the increase in feed and depth of cut led to a continuous rise in the level of residual stresses.
It is also worth noting that the internal residual stress distributions of different types of metallic materials show specific patterns of change after undergoing the CNC machining process.
These research results provide valuable references for improving the CNC machining technology of metallic materials and enhancing the performance and stability of the final products.
Comparison of residual stress values under different cutting speeds, as shown in Table 1.
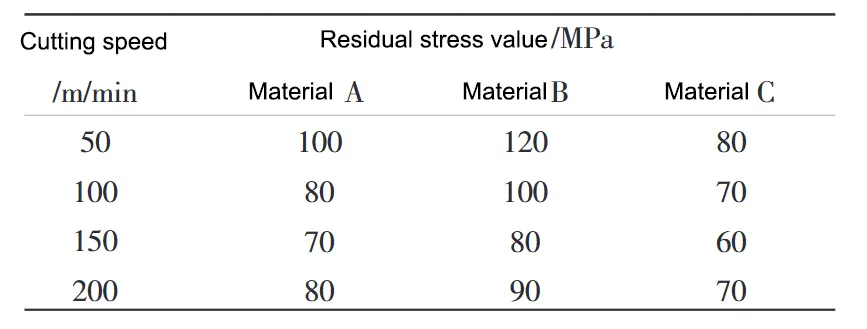
Residual Stress Relief Methods
1. Heat treatment method
Annealing is a commonly used method to eliminate residual stresses, and it is essential for optimizing metals’ microstructure and properties.
The method involves heating the metal to a specific temperature range and maintaining it at this condition for a certain period. This is followed by a slow cooling down to promote the effective release and elimination of stresses within the material.
The specific temperature and annealing holding time must be set accurately for different types of metals and their processing history.
Tempering, on the other hand, is a heat treatment step carried out after quenching to reduce residual stresses caused by quenching.
It involves reheating the quenched metal to a specific temperature, holding it for a certain period, and then cooling it down to reduce residual stresses caused by quenching. Tempering also enhances the toughness and ductility of the material to ensure that it is more robust and durable.
The choice of tempering conditions directly affects the quality of the final product.
Ageing, on the other hand, is a slower process that gradually adjusts and releases internal stresses by storing the metal at room or preset temperatures for an extended period of time.
Determining the appropriate aging cycle based on the metal material and its pre-processing is particularly effective in improving the material’s long-term stability and fatigue resistance.
2. Mechanical treatment method
Shot peening is a technology that applies force to the surface of the metal material using high-speed spraying of projectiles, which leads to plastic deformation of the metal surface.
This plastic deformation helps eliminate the residual stresses in the material and can effectively improve its surface hardness and fatigue strength.
After this type of treatment, the performance of the metal material is enhanced in various aspects.
On the other hand, rolling uses rollers to apply pressure to the surface of the metal material, causing it to undergo a plastic change, thereby reducing the internal residual stresses.
This method increases the material’s surface hardness and significantly improves its smoothness.
The surface quality and smoothness of metal products after the rolling treatment significantly improve.
Tensile treatment is a technique in which the metal is subjected to specific tensile stress conditions for extension.
This process helps release stresses within the material, optimizing its internal structure.
Tensile processing is essential for improving the dimensional and shape accuracy of materials in the precision manufacturing sector. Metals subjected to this treatment will have significantly improved dimensional and morphological accuracy.
3. Vibration treatment
The vibration treatment method is a kind of specific equipment. The metal material is placed on the vibration table, and the vibration generated by the vibration table acts on the material to release its internal stress.
This method can effectively optimize the microstructure of the metal material and then improve its comprehensive performance.
Particularly effective in improving the fatigue strength of the material because the vibration process, the internal cracks and defects in the material to a certain degree of healing and repair, thus enhancing the ability of the material to resist fatigue damage.
In addition, vibration treatment also helps to improve the material’s resistance to stress corrosion characteristics, which is attributed to vibration’s ability to relieve the material surface and the internal region of the stress concentration situation, thereby reducing the possibility of stress corrosion under corrosive conditions.
In summary, vibration treatment, as an effective metal strengthening process, not only enhances the material’s mechanical properties but also extends its service life, showing a broad development potential in practical applications.
By adopting appropriate elimination methods, residual stresses can be effectively reduced, and the dimensional accuracy, fatigue strength, and surface quality of metal materials can be improved.
Different elimination methods have different advantages and disadvantages. In practical applications, they should be selected according to the type of material, processing technology, performance requirements, and other factors, such as the effect of elimination methods on the performance of metal materials, as shown in Table 2.

Conclusion
The article studied the residual stress distribution and elimination methods of CNC machining of metal materials.
It discussed the mechanism of residual stress and its distribution law in depth by analyzing the influence of CNC machining parameters on residual stress, combined with experimental research and numerical simulation.
The research results show that the cutting parameters significantly influence the residual stress, and the residual stress distribution of different metal materials after CNC machining is different.
Selecting appropriate residual stress relief methods can effectively improve the quality of CNC machining of metal materials and extend the service life of parts.
Future research can further explore the mechanism of residual stress, optimize the residual stress relief methods, and improve CNC machining technology.