Table of Contents
CNC turning centers, a type of high-efficiency, precise, and multifunctional machining equipment, are increasingly important in the production of complex parts.
However, since complex parts are often characterized by complicated structures and high process requirements, they often face many challenges in the design and machining process.
Meeting the performance requirements of parts while taking into account factors such as machining efficiency, precision, and cost has become a key issue to be solved in the field of CNC turning.
Aiming at the difficulties in the structural design of complex parts in CNC turning centers, scholars have carried out a lot of research.
Modular design, topology optimization, parametric modeling and other methods are widely used in the optimization design of complex parts structure, and certain research results have been achieved.
However, combining these advanced methods with practical engineering applications remains a challenge.
It still requires in-depth exploration of theory and practice to further enhance the manufacturing level of complex parts in CNC turning centers.
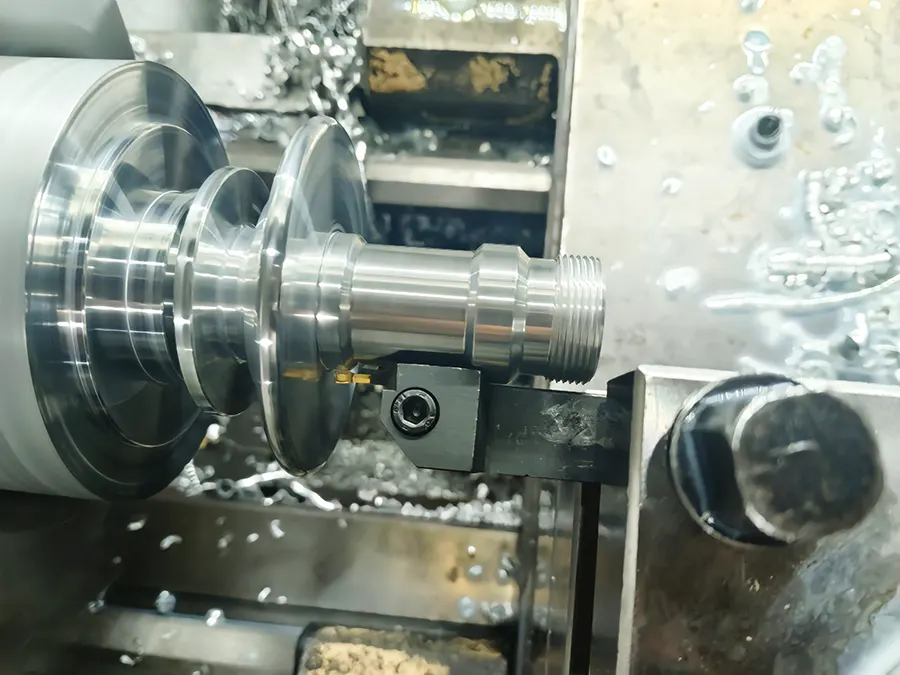
CNC turning center complex parts structure design needs
In the field of CNC turning center machining, the structural design of complex parts faces multiple needs and challenges.
First of all, complex parts usually have a variety of functional structures, such as transmission, sealing, lubrication, heat dissipation, etc.
These functional structures need to realize a reasonable layout and integration in a limited space to ensure the overall performance of the parts.
Secondly, complex parts are often subjected to alternating loads and stresses in the service process.
Therefore, the rigidity and strength of the parts must be taken into account in the structural design.
The mechanical properties of the parts should be improved through reasonable material selection, dimensional optimization, and topological layout.
This will ensure the reliability and stability of the parts under complex working conditions.
In addition, the complex parts machined by CNC turning centers usually have complicated internal cavity structures, such as deep holes, cross holes, and variable cross-section holes.
These features put forward higher requirements for tool feed path planning and cutting parameter optimization.
The design of complex internal cavities must not only consider the feasibility of machining but also take into account the assembly accuracy and service life of the parts.
In addition, the structural design of complex parts requires comprehensive consideration of the manufacturability and economy of production.
On the one hand, the parts’ structure should be adapted to the machining characteristics of CNC turning centers.
This will minimize the use of non-standard tools and special fixtures, reducing machining difficulty and manufacturing costs.
Reasonable structural decomposition and modular design can improve the versatility and interchangeability of parts and shorten the product development cycle.
In short, the structural design of complex parts of CNC turning centers needs to be systematically weighed and optimized in multiple dimensions, such as functionality, reliability, technology, and economy.
This is essential to achieve the goal of high-quality, high-efficiency, and low-cost manufacturing.
Common types of complex parts structure
In the field of CNC turning center machining, the structural types of complex parts present diverse characteristics.
Among them, thin-walled lightweight structure is widely used in aerospace, automotive, electronics and other industries.
By reducing the wall thickness of the parts and adopting the layout of skin reinforcement, the strength and rigidity of the parts are ensured.
At the same time, the mass is greatly reduced, which is crucial for improving the equipment’s power performance and transport efficiency.
At the same time, complex parts made of hard and difficult-to-machine materials, such as titanium alloys and high-temperature alloys, perform well under extreme operating conditions.
However, due to their excellent specific strength and high-temperature resistance, they also pose many challenges for cutting, requiring targeted optimization of tool materials, cutting dosage, and machining strategies.
Another typical category of complex parts are those with special structures such as deep cavities, narrow holes and irregular internal cavities.
These “hard-to-machine structures” place higher demands on tool accessibility and cutting fluid lubrication and cooling.
They often require specialized processes, such as small aspect ratios, high-pressure cooling, and vibration-assisted machining, to improve surface quality and dimensional accuracy.
The surface quality and dimensional accuracy can be improved.
It is worth mentioning that, with the development of 3D printing technology, some complex-shaped structural parts adopt the composite processing method, which combines additive and subtractive manufacturing.
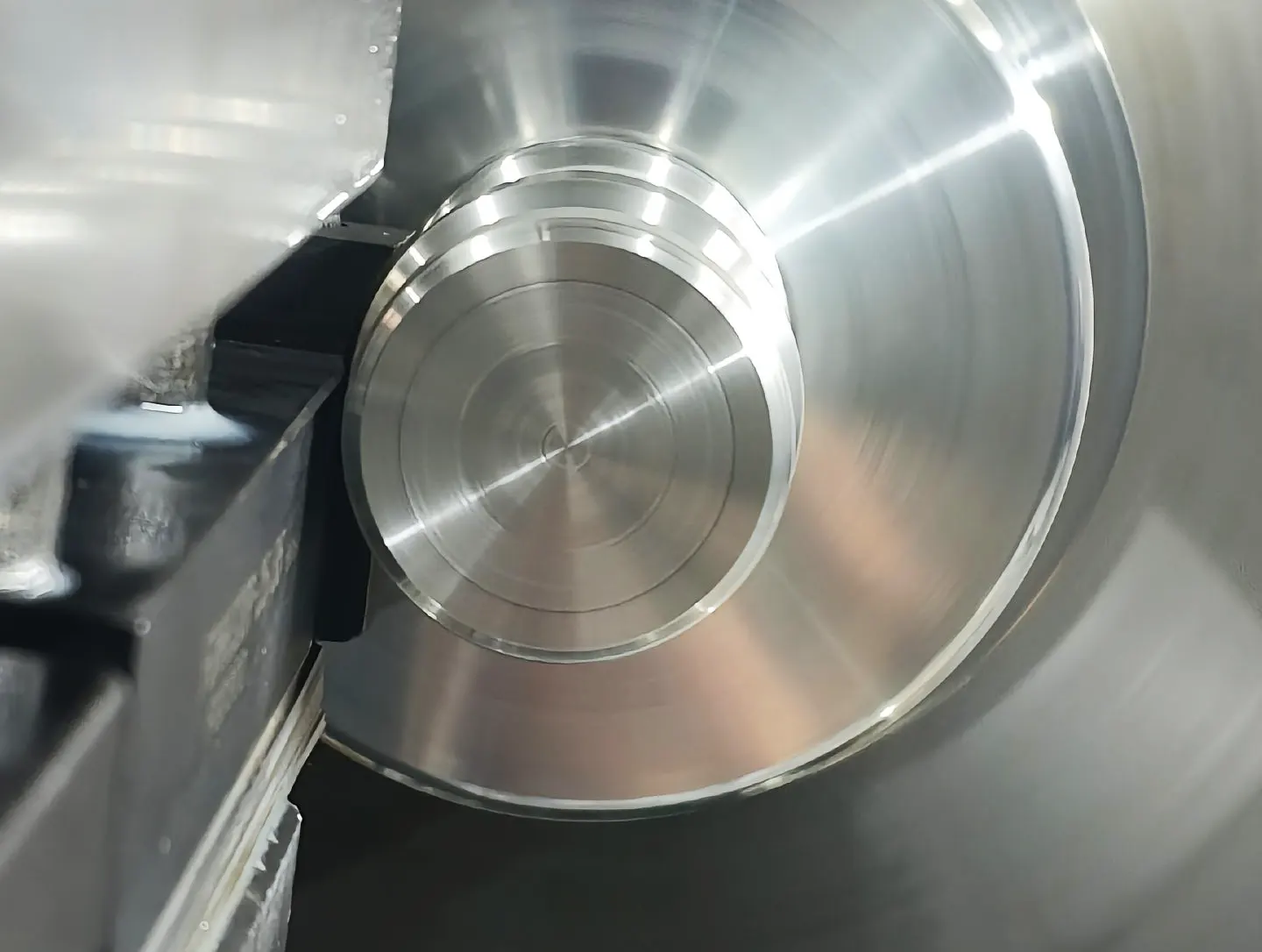
This method uses 3D printing to shape the complex internal structure. It then improves the accuracy of the key surfaces through CNC turning, realizing a degree of freedom in structural design that is difficult to achieve with conventional processing..
CNC turning center complex parts structure design difficulties
Multi-functional structure integration
Multifunctional structure integration is a difficult problem to overcome in the structural design of complex parts of CNC turning centers.
Modern mechanical products often need to realize transmission, sealing, heat dissipation, vibration damping, and other functions in a limited space, which puts higher requirements on the internal structure of parts.
According to statistics, every time the complexity of a part’s structure increases by an order of magnitude, its functional integration will increase by 1.5 to 2 times. However, the volume utilization rate shows a significant decline.
The integrated design of multifunctional structures requires in-depth theoretical analysis and numerical simulation in multi-disciplinary fields such as mechanics, thermodynamics, and fluid dynamics.
This is necessary to reveal the coupling mechanism and mutual influence law between different functional structures.
However, due to the irregular geometry and large-scale differences in the internal structures of complex parts, traditional numerical methods often encounter bottlenecks.
These include difficult mesh delineation and huge computational volume in the modeling and solution process, making it challenging to obtain high-precision multi-physics field distribution results
Meanwhile, the integration of multifunctional structures involves many factors, such as material selection, surface treatment, and connection methods, etc.
The influence mechanism of different materials and processes on the performance of the parts is still unclear, and reliable theoretical guidance and empirical data are lacking.
Therefore, realizing the optimal integration of multifunctional structures while considering functionality, reliability, and manufacturability is crucial.
his has become one of the key bottlenecks restricting the innovative design of complex parts
Stiffness-strength balance
Complex parts of CNC turning centers are generally subjected to alternating loads and complex stresses during service.
Therefore, achieving the optimal balance of part stiffness and strength within the limited design space is an urgent problem to be solved.
From the nature of mechanics, the stiffness reflects the ability of the part to resist deformation, while the strength characterizes the limit level of parts to resist damage.
Increasing the stiffness and strength of a part often requires an increase in cross-section size or the use of high-strength materials, but this inevitably leads to a significant increase in part quality and cost.
In the lightweight design of complex parts, if the blind pursuit of stiffness and ignore the strength of the part in the fatigue load will shorten the safe life of the part by more than 60%;
On the contrary, if strength is emphasized unilaterally and the rigidity constraint is relaxed, the parts’ dynamic response characteristics will significantly deteriorate.
Therefore, the CNC turning center complex parts’ stiffness-strength balance design must consider multiple objectives.
These include static and dynamic performance, safety and reliability, as well as lightweight characteristics, requiring trade-offs and optimization.
However, due to material anisotropy, geometrical irregularities, and randomly varying load spectra of complex parts, it is extremely challenging to characterize their force state accurately.
This is especially difficult under actual working conditions.
The traditional design methods based on empirical coefficients and safety margins are difficult to meet the increasingly stringent requirements.
There is an urgent need to develop advanced design theories and methods, such as topology optimization for working conditions.
Complex Internal Cavity Design
The design of complex internal cavities is a very challenging problem in the structural design of complex parts of CNC turning centers.
As the negative space inside the part, the internal cavity usually performs many functions, such as oil and air conduction, weight reduction, and heat dissipation.
Its structure and dimensional accuracy have a decisive influence on the part’s performance and reliability.
However, due to the complex characteristics of the internal cavity structure, such as long, narrow, curved, intersecting, and variable cross-sections, it isn’t easy to generate high-quality geometric and analytical models.
The traditional orthogonal mesh discretization method seriously restricts the internal cavity structure’s parametric design and simulation optimization.
In addition, due to the lack of external features that can be directly measured and evaluated, it isn’t easy to quickly and accurately obtain key performance parameters.
Under the internal cavity structure’s service state, these parameters include stress-strain, temperature field, flow field, and others.
This presents a great challenge to characterization of the internal cavity structure’s mechanical behavior and analysis of the failure mechanism.
The design of complex internal cavity structures requires the cross-fertilization of knowledge from multiple disciplines.
These include mechanics, heat transfer, and fluid dynamics, among others.
This is a significant challenge to the existing theoretical basis, construction, and design of internal cavity structures.
This puts forward higher requirements on the existing theoretical foundation, modeling simulation tools and optimization design methods.
Optimization of the structural design of complex parts for CNC turning centers
Modular design method
Modular design is an essential method for optimizing complex parts’ structure in CNC turning centers.
The core idea of this method is to systematically decompose complex parts based on their functional and structural characteristics.
It involves dividing them into several relatively independent yet interrelated functional modules and defining standardized interface specifications.
This approach enables the design of each functional part to be standardized, serialized, and generalized, ensuring consistency and efficiency in complex part development.
Through modularization design, complex parts present a clear hierarchical structure:
The top level represents the overall functional requirements of the part.
The middle level focuses on the structural layout and interface definition of each functional module, while the bottom level specifies each module’s detailed structural parameters and processing technology.
This hierarchical structure is conducive to decoupling and reorganizing the internal functions of the part.
It also improves design flexibility, maximizes the reuse and sharing of manufacturing resources, and significantly shortens the product development cycle while reducing costs.
FIrst step is to apply function analysis and function decomposition methods in the modularization design process.
This helps identify the parts’ basic functional units, which can then be further divided into several independent functional modules.
When dividing the modules, we should ensure the integrity and independence of each module’s functions.
At the same time, we need to consider the correlation and coupling between them, ensuring that the modularized structure can be assembled and integrated smoothly.
Secondly, designers need to start at the structural level after defining the modules’ demarcation and interface.
They should use 3D CAD and other software for each functional module’s geometric and parametric modeling.
Additionally, they must clarify the design parameters of the module’s internal structure and the topological relationships between modules.
By strictly following the predefined interface standards, they can achieve virtual assembly and flexible combination of modular parts.
Finally, after completing the module structure design, it is necessary to match and optimize each module’s manufacturing resources and machining scheme from the process level.
CNC turning centers are characterized by multi-axis linkage and compound machining, but they also require higher tools, fixtures, cutting parameters, and other resources.
Therefore, designers must fully consider CNC turning equipment’s processing capacity and process characteristics and reasonably plan the module’s machining sequence and cutting path.
At the same time, optimizing the geometric parameters of cutting tools and material grades helps improve machining accuracy and surface quality.
Additionally, it reduces the need for customized non-standard fixtures and enhances the versatility and reusability of manufacturing resources.
Application of topology optimization technology
Topology optimization is a structural optimization design method that seeks for the optimal material distribution.
By discretizing the structural design domain and introducing the material phase function, the optimal topology configuration of material distribution is determined under the constraints of load boundary conditions.
This approach enables the maximization of structural rigidity or the minimization of flexibility.
Introducing topology optimization technology into the lightweight design of complex parts in CNC turning centers can effectively solve the stiffness-strength balance problem.
It achieves this by obtaining an ideal material distribution and force transfer paths while ensuring the stiffness and strength of the parts.
Specifically, the topology optimization design is divided into the following key steps:
First, the optimization objective function is selected reasonably, such as the minimum flexibility design, commonly used to minimize the strain energy as the objective function.
In contrast, the maximum stiffness design maximizes the overall structural stiffness as the optimization direction.
Conclusion
The structural design and optimization of complex parts in CNC turning centers demand a thoughtful integration of advanced engineering strategies.
Through the application of modular design, manufacturers can achieve greater flexibility, ease of assembly, and maintenance efficiency.
Meanwhile, the incorporation of topology optimization allows for significant material savings and performance improvements by refining part geometry based on actual load paths and constraints.
When combined, these approaches not only improve the mechanical performance and manufacturability of components but also reduce production costs and development cycles.
As CNC technology continues to evolve, embracing such innovative design methods will be critical to maintaining competitive advantage in precision manufacturing.