With the rapid development of CNC machining technology, CNC tooling as an important part of CNC machining, its selection of processing quality and efficiency has a significant impact.
Many experts and scholars have analyzed and studied the various aspects of CNC machining to improve its precision, control its cost, and increase its efficiency.
The purpose of this paper is to analyze the impact of CNC tool selection on the CNC machining process by reviewing the relevant literature, providing a reference for research and practice in the field of CNC machining.
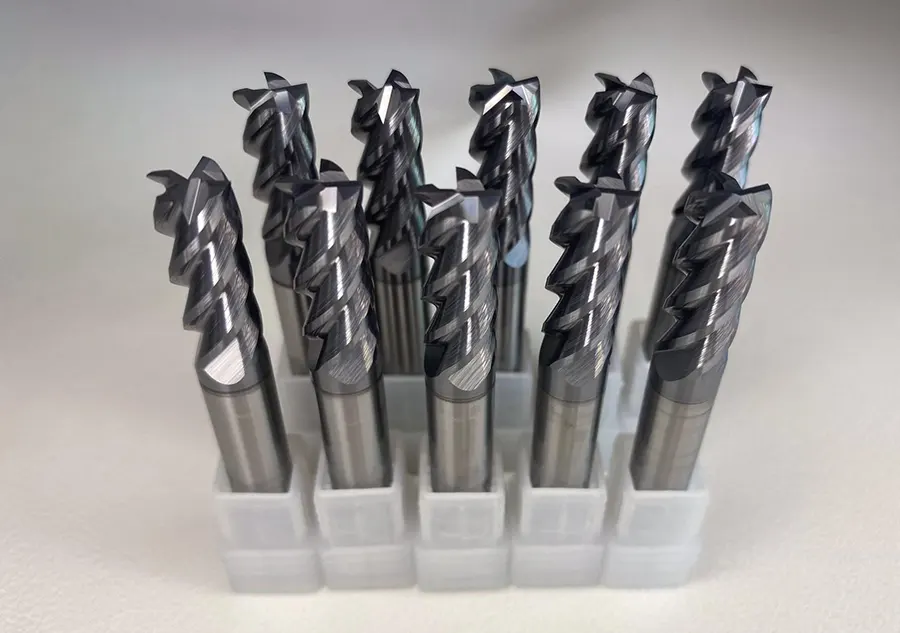
Problems in the use of CNC tools
Cutting volume can not be optimized
Cutting volume is the main factor affecting machining efficiency and machining accuracy.
Lack of experience and ability prevents operators from scientifically calculating the optimal cutting amount, which reduces processing efficiency. Selecting the appropriate cutting amount is key to CNC production.
Excessive tool wear
Reasonable tool selection and use can improve workpiece processing quality, increase the tool’s service life, and reduce production costs.
However, in actual production, operators often fail to select the proper tool, leading to increased wear and even chipping or breaking, which raises processing costs.
CNC tool types and characteristics
CNC tools are the core of CNC machining. They realize the cutting function of important parts and adapt to different processing requirements and processing technology.
Thus, there are a variety of CNC tool types, and classification is also many ways, as shown in Table 1, for the common classification of CNC tools and common tools.
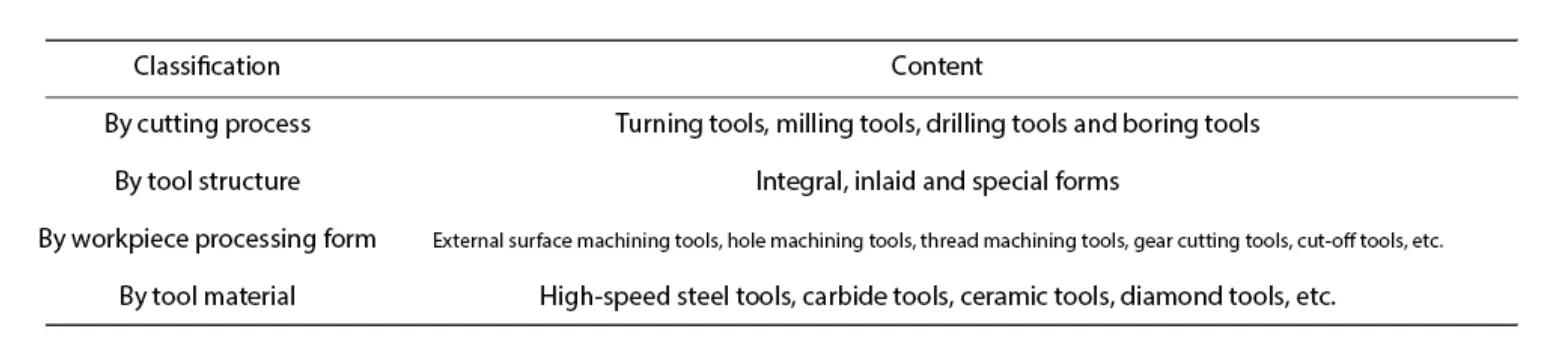
Different material types of tools have different tool characteristics and scope of application, as shown in Table 2, for the common tool materials and application scenarios.
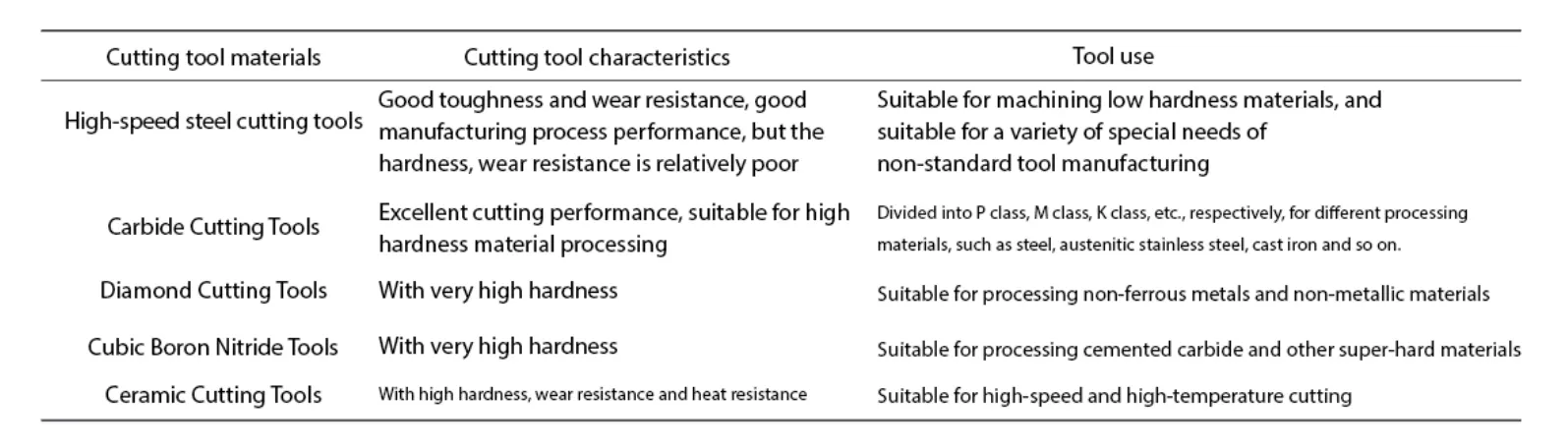
CNC tool selection on the impact of the machining process
Impact on machining accuracy
Machining accuracy is an essential indicator of the quality of CNC machining.
Tool geometry, material and manufacturing process directly determines the machining accuracy and surface quality of parts.
Different tool materials have different hardness, wear resistance, and toughness, as well as different tool edge shapes, tip radius, and cutting angles. These have an important impact on the cutting force, cutting heat, and the shape of the resulting chips, which in turn impacts the machining accuracy and surface roughness.
As shown in Table 3, it is suitable for machining workpiece materials of various tools.
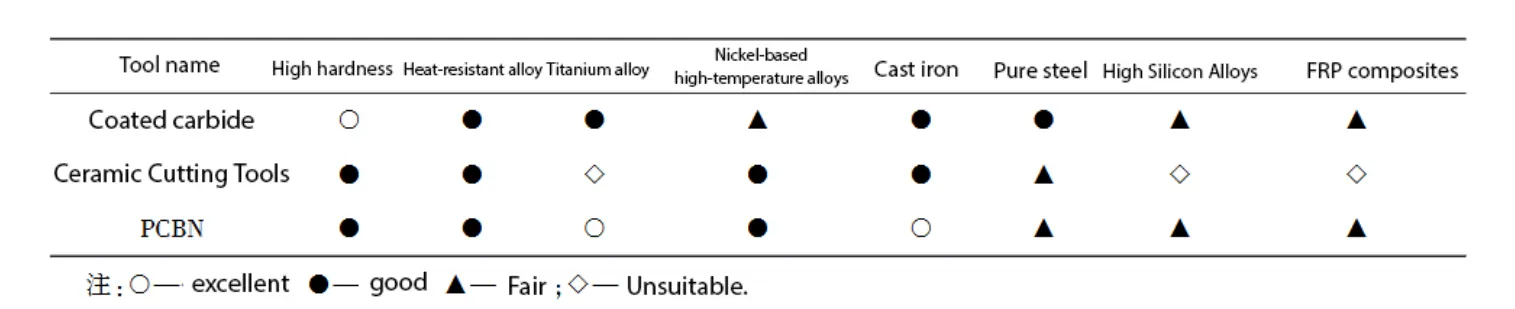
Reasonable tool selection can effectively reduce cutting force, cutting heat and vibration, thus improving machining accuracy.
Impact on machining efficiency
Machining efficiency is an important indicator for evaluating the economic benefits of CNC machining.
Tool cutting speed, feed, and depth of cut, and other parameters of reasonable choice, can improve machining efficiency and reduce processing time.
Analyzing the impact of different tool materials on cutting speed, feed, and depth of cut, we found that carbide tools have higher cutting performance than high-speed steel tools and can significantly improve machining efficiency.
In addition, tool durability, geometry and parameter optimization also help to improve machining efficiency.
Impact on machining cost
Machining cost is an important factor that the enterprise needs to consider when selecting CNC tools.
The price of the tool directly affects the cost of machining. Comparing the cost-effectiveness of different tool materials, types, and brands found that choosing the right tool can reduce the cost of machining while ensuring the quality of machining.
In addition, tool life and tool materials, cutting parameters and processing conditions, etc., a reasonable choice of tools can reduce tool consumption costs.
At the same time, the reuse of tools and edge repair technology also helps to reduce processing costs.
CNC tool selection factors to consider
When selecting CNC machining tools, one should fully consider the relevant factors affecting.
1) the nature of the production of tool processing.
2) the type of machine tool, machine performance, and machine power, speed and rigidity, etc.; 3) CNC machining design planning program.
3) CNC machining design planning program.
4) Requirements such as workpiece size, basic shape, surface roughness, workpiece accuracy, etc., which determine the type and parameters of the tool; and
5) The material properties of the machined workpiece, different workpiece materials need to choose different tool materials and geometries.
Therefore, according to the actual working conditions, combined with various factors to consider, select the most suitable tool for processing.
Reasonable use of tool optimization measures
Selection of suitable tools and scientific process parameters
CNC machining, according to the design drawings, involves developing a scientific and reasonable processing technology to determine the process parameters, but also needs to choose the right tool according to the material, processing equipment, and other factors, in order to improve the efficiency of tool use and its life.
Select the appropriate clamping force
CNC machining process, the tool through the screw mounted on the equipment. The tool is screwed onto the machine and fixed in place.
After completing the installation, operators should calculate the tool’s clamping force to ensure it falls within a reasonable range.
This will prevent the blade from cracking, loosening, shifting, etc., which will affect the machining accuracy.
Reduce tool vibration
The tool must be controlled to improve its stability in the cutting process and ensure machining accuracy. The necessary measures must be taken to reduce vibration, such as choosing a reasonable tool clamping method and adjusting the spindle speed.
Reduce vibration helps to extend the service life of the tool, protect the machine tool.
Full use of coolant
Cutting heat is common in CNC machining factors affecting machining accuracy, the reasonable use of coolant, can reduce the operating temperature of the tool, reduce tool wear, improve the efficiency of tool use and life, to ensure machining accuracy.
Common cooling methods: coolant spray cooling, coolant immersion cooling, and do not use any coolant, the use of air cooling gas cooling.
Development of new tools, research, and development of new production processes
Increase the research and development of new tools, making timely investments so that the tool’s performance can meet the requirements of new machine tools.
Research and develop new machining processes and adopt new machining methods to reduce the processing time of complex parts and the number of tools used.
Conclusion
CNC tool selection has an important impact on the CNC machining process. Reasonable tool selection can not only improve machining accuracy and efficiency but also reduce processing costs.
At the same time, machine accuracy, cutting parameters, tool selection, and other factors need to be considered to improve machining accuracy.
Intelligent manufacturing technology can help monitor and control the machining process.
Therefore, in CNC machining, selecting suitable tool types and parameters should be based on the processing needs and material characteristics.
In the future, with the continuous development of new materials, processes, and technologies, CNC machining and machining accuracy will hopefully achieve higher breakthroughs and development.