Precision Metal and Plastic Parts, Made Just for You
Die casting service
Our offers substantial advantages compared to other manufacturing processes, resulting in significant cost savings not only in the part price but also in overall production costs.
- Achieving variable wall thicknesses
- Attaining tighter tolerances
- Significantly reducing production cycle times
- Minimizing material scrap
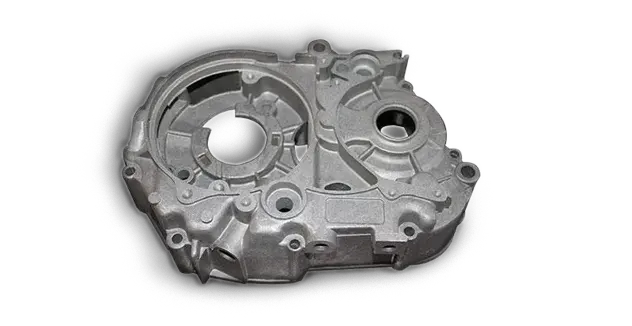
Start A Casting Quote
step | stp | stl | igs | iges | obj
All uploads are secure and confidential.
Type of Die Casting Services
Streamlining the manufacturing process with fewer steps from raw material to finished part.
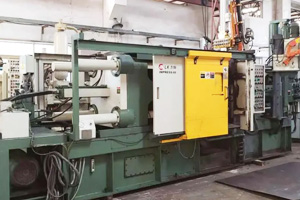
1. Hot-Chamber Die Casting
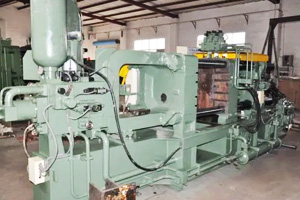
2. Cold-Chamber Die Casting
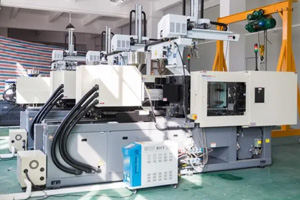
3. Injected Metal Assembly
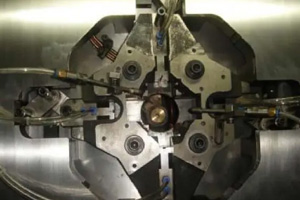
4. Multi-Slide Die Casting
Our Advantages
Speed
Lorem ipsum dolor sit amet, consectetur adipiscing elit. Ut elit tellus, luctus nec ullamcorper mattis, pulvinar dapibus leo.
Quality
With multiple quality checks throughout the production process to ensure the final product meets your specifications.
Materials
We offers a wide variety of materials to choose from, including metals, plastics, and composites, to suit different applications.
Prototyping
We offers prototyping services, allowing you to test and refine your design before moving to full-scale production.
Die Casting Tolerance and Capacity
“We provide CNC turning services for over 100 types of metal, ensuring high precision and quality for all your machining needs.”
Tolerance |
|
---|---|
Linear tolerances | ±0.05mm |
Angular tolerances | ±0.05mm |
Surface tolerances | ±0.1mm |
Shrink Mitigation | ±0.15mm |
Holes | ±0.2mm |
Over 400mm to 1000mm | ±0.4mm |
Over 1000mm to 2000mm | ±0.5mm |
Capacity |
|
---|---|
Min Part Size | ±0.05mm |
Max Part Size | ±0.05mm |
Max Part Weight | ±0.1mm |
Minimum wall thickness | ±0.15mm |
Mould Life | ±0.2mm |
Delivery Time | ±0.4mm |
Design Guidelines
Optimize your designs for manufacturability with our expert guidance and feedback, ensuring superior results in sheet metal fabrication.
Keep wall thickness uniform for consistent cooling and solidification. Ideal thickness: 1.5 mm – 6 mm, but this can vary depending on the material.
Wall Thickness
Use draft angles to allow easier removal of the part from the die.
Standard draft angle: 1° to 3° (more for deeper cavities).Draft Angles
Rib thickness should be 50% of wall thickness to avoid casting defects.
Use ribs and gussets to reinforce thin walls and reduce part deflection.
Ribs and Gussets
Use rounded fillets and larger radii to avoid stress concentrations, improve metal flow, and reduce cracking.
Fillets should have a minimum radius of 0.5–1 mm.Fillets and Radii
Account for shrinkage during solidification, especially for aluminum and zinc alloys.
Shrinkage rates vary by material, so ensure your design compensates for this.Casting Shrinkage
Plan for an effective ejection system to ensure smooth removal from the die.
Consider ejector pins or bladders for complex geometries or delicate features.Ejection System Design
Design cores and cavities to ensure proper cooling channels and even metal flow.
Use cooling channels near thick sections to control the temperature and reduce cycle time.Core and Cavity Design
Ensure proper venting for the mold to allow air to escape during filling and reduce gas entrapment.
Vent size should be 0.1 mm to 0.3 mm in diameter.Ventilation
Die Casting Materials
“We provide a diverse selection of materials for high-pressure die casting, ensuring the ideal match for your unique application requirements.”