CNC machining technology, one of the core technologies of modern manufacturing, has been widely used in machining, automobile manufacturing, and other fields. The emergence of CNC machining technology not only greatly improves processing accuracy and efficiency and reduces production costs but also promotes the transformation and upgrading of the machining industry toward digitalization and intelligence.
In machining, specific work requirements and scientific application of CNC machining technology should be combined to fully exploit the advantages of CNC machining technology.
CNC machining technology
CNC machining technology is a highly automated manufacturing technology, the core of which lies in the use of computer numerical control system to accurately control the movement of the machine tool and the machining process, the technology integrates computer technology, automatic control technology, sensor technology and machining technology and other areas of results, is the modern manufacturing industry to achieve high precision, high efficiency, high quality machining of important means.
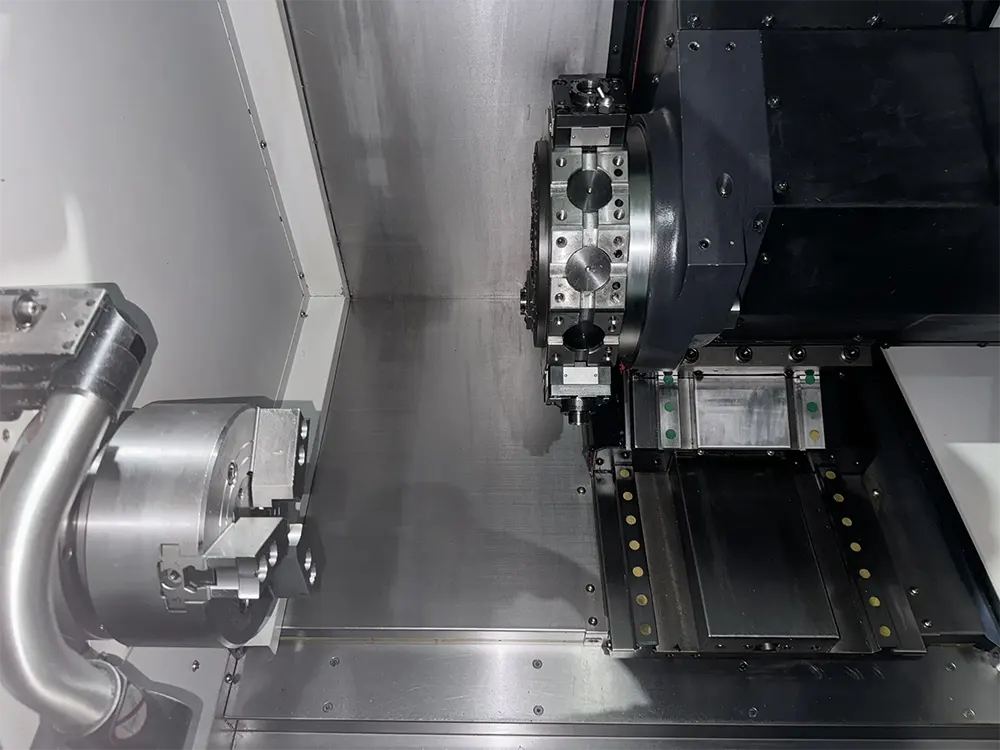
The basic principle of CNC machining technology is that the various movements and operations in the machining process are pre-set in the computer through programming, and then use the CNC system to convert these instructions into control signals that can be recognized by the machine tool, thereby controlling the machine tool’s various axes of motion, cutting tools, fixtures and other components to achieve automated machining of the workpiece.
This kind of processing method has a very high degree of flexibility and precision, can adapt to a variety of complex and changing processing needs, its main features include high precision, high efficiency, wide range of processing, flexibility and automation degree.
Advantages of the application of CNC machining technology in machining
(1) improve processing accuracy and efficiency
CNC machining technology through accurate CNC programming and machine control, can achieve micron or even nano level machining accuracy, greatly improving the machining accuracy of the workpiece.
At the same time, CNC machining technology can greatly improve processing efficiency, shorten the production cycle, the traditional mechanical processing often requires multiple clamping and adjustment, while CNC machining technology can be completed through a clamping multiple processes, reducing the processing time and waiting time.
(2) Reduce labor intensity and labor costs
CNC machining technology has realized the automation and intelligence of processing, greatly reducing the labor intensity of the operator. Operators only need to program and simple operation, you can complete complex processing tasks, avoiding the traditional machining requires a lot of manual operation and adjustment.
In addition, CNC machining technology can also reduce the number of operators and reduce labor costs, thereby reducing the operating costs of enterprises.
(3) to adapt to the complex and changing processing needs
CNC machining technology has a high degree of flexibility and adaptability, and can cope with a variety of complex and changing processing needs. Through programming and control, CNC machining technology can realize the processing of various shapes and structures of workpieces to meet the processing needs of different fields. At the same time, it can also realize the processing of different materials and different processes, further expanding its scope of application.
CNC machining technology in machining applications
1. CNC technology in the processing of plexiglass transparent parts application
Plexiglass transparent parts with high transparency, easy to process and other advantages, widely used in a variety of fields, but most of the transparent parts of the structure is relatively loose, in the processing of molecular movement is too violent will lead to material cracking.
In the field of transparent parts processing, the integration of advanced numerical control technology to use the appropriate processing parameters, significantly improves the processing efficiency, precision, and quality of glass transparent parts, and effectively controls the material blow-up during processing.
CNC lathe uses a computer numerical control system to control the movement of the machine tool and the machining process, as shown in Figure 1, according to the pre-programmed CNC program, accurate control of the tool relative to the workpiece trajectory, cutting speed, and depth of cut, so as to achieve high efficiency and high precision machining of acrylic and other plexiglass transparent parts.
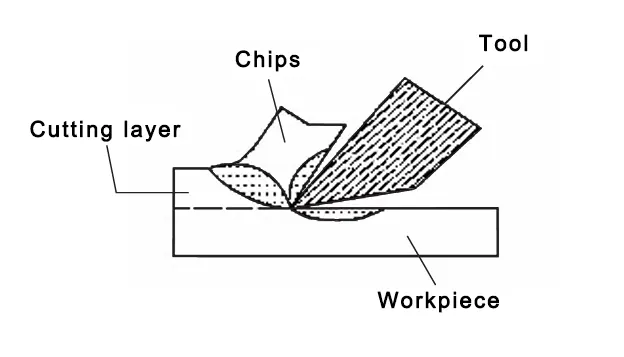
Figure 1 cutting speed and plastic deformation relationship
In actual processing, CNC machining can be based on the nature of different glass materials and processing requirements, precise control of cutting speed, feed and depth of cut and other parameters, to ensure that the plastic deformation of the processed workpiece is reduced, through the programming software, you can optimize the tool path to reduce the empty stroke and invalid cutting.
In addition, CNC machine tools have good flexibility and adaptability, can quickly respond to product changes and changes in processing requirements, through the replacement of tools, adjust the program and parameters, etc., can achieve different specifications, different shapes of plexiglass transparent parts processing.
2. Application of CNC milling machine in complex surface machining
In the field of machining, complex surface machining has always been a technical challenge. Complex surface machining involves a variety of shapes and sizes of surfaces, these surfaces often require high precision and high finish, in addition, also need to consider the hardness of the material, tool selection, cutting force control, and other factors, all of which may affect the processing quality and efficiency.
CNC milling machine is a highly automated machine tool, through the computer numerical control system according to the pre-programmed machining program to control the rotation of the milling cutter and the machine tool’s multiple axes of movement, precise control of the path of the milling cutter, cutting speed and depth of cut, to achieve a variety of materials and shapes [2] shape of complex surfaces milling processing.
CNC milling machines are usually equipped with high-speed spindles and large-capacity tool magazines, which can realize rapid and continuous processing and significantly improve production efficiency, and technicians can change the processing program to make CNC milling machines quickly adapt to different processing needs and reduce production preparation time.
3. CNC machining center in the application of multi-process compound processing
The CNC machining center as an important equipment in the field of modern machining, which plays an irreplaceable role in multi-process compound machining, CNC machining center integrated milling, turning, drilling, tapping, and other machining functions in one, and its high-precision, high-efficiency machining characteristics make it become the preferred equipment for complex parts processing.
CNC system according to the pre-programmed machining program, controls the spindle rotation, tool replacement, and the use of coolant, so as to complete a variety of complex cutting and machining operations.
The tool magazine of the CNC machining center can store a variety of tools, and through the automatic tool changer device achieve rapid tool replacement, in a single clamping to complete a number of work [3] sequence of machining.
Multi-process compound machining refers to a machine tool, through a clamping to complete a number of machining processes, so as to achieve the overall processing of the workpiece, the processing mode requires a high degree of flexibility and stability of the machine tool to adapt to the processing needs of different processes, while the workpiece clamping needs to have the accuracy and reliability to ensure the stability and safety of the machining process.
CNC machining centers with its high degree of automation and intelligence, in the multi-process compound processing advantages:
① Significantly improve productivity and reduce the workpiece clamping and change over time;
② CNC machining center’s high-precision control capabilities to ensure machining accuracy and improve the overall processing quality;
③ processing a wide range of high flexibility, easy-to-realize automated production and so on.
4. CNC cutting in precision parts processing applications
In the processing of plexiglass transparent parts, CNC cutting technology can process small holes and complex shapes parts, but also with other processing methods such as grinding, polishing, etc., to further improve the processing accuracy and surface quality of glass transparent parts.
Through precise CNC programming and machine control, micron-level precision control of the workpiece can be achieved, realizing high-precision and high-efficiency cutting processing.
When processing glass lenses with complex curved surfaces, a CNC milling machine with five-axis linkage function that can realize high-speed cutting, a carbide tool suitable for processing glass, and a coolant system are selected to reduce the cutting temperature.
In the processing process, the use of CNC milling machine real-time monitoring of the processing accuracy and surface quality of the lens, if deviations or problems are found, compensation and adjustment are immediately carried out, CNC equipment can ensure that each glass lens can meet the design requirements.
Measures to improve the technical level of mechanical CNC machining
1. Optimize the mechanical CNC machining control structure
Optimization of mechanical CNC machining control structure is the basis for improving the level of machining technology, on the one hand, it is necessary to establish a perfect machining process management system, clear responsibilities and workflow of each link.
On the other hand, strengthen the monitoring and scheduling of the machining process to ensure the stability and controllability of the machining process, the introduction of advanced CNC machining management system, through information technology means to achieve comprehensive management and optimization of the machining process.
2. Select the appropriate machine tool
Selection of suitable machine tool is essential to improve machining accuracy and efficiency, you need to select the appropriate type and specification of the tool according to the nature of the processed material, machining accuracy and machining efficiency requirements, according to the material of the workpiece to select the appropriate milling cutter, see Table 1.
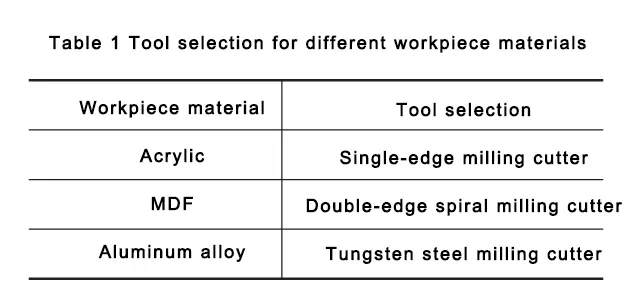
Table 1 Corresponding tool selection for different workpiece materials
At the same time, it is necessary to check the tool regularly to ensure the sharpness of the tool, replace the tool beyond the service life in a timely manner, and strengthen the management and maintenance of the tool to avoid damage and waste of the tool.
3. Strengthen the professional level of programming personnel
CNC programming is the core link in mechanical CNC machining, strengthening the professional level of programming staff is one of the key measures to improve the technical level of mechanical CNC machining.
① Regularly carry out such as basic theory of CNC programming, advanced programming software skills, machining process optimization and other aspects of professional training activities, so that programmers continue to master the new programming techniques and methods to improve programming efficiency and accuracy.
②Actively introduce high-quality talents to bring new ideas and methods for mechanical CNC machining, stimulate the team’s vitality, and promote the overall level of the team [5] .
③ In the process of mechanical CNC machining, the cooperation and communication between the programmers and the personnel in other positions should be strengthened, a good teamwork mechanism should be established, and the transfer of knowledge and the accumulation of experience between the team should be promoted through regular exchange meetings and technology sharing, so as to jointly improve the technical level of mechanical CNC machining.
4. Improve equipment maintenance, maintenance measures
In order to ensure the normal operation and extend the service life of the equipment, it is necessary to establish a perfect equipment maintenance system, the system should clearly stipulate the daily maintenance of the equipment, regular maintenance and special maintenance, etc., to ensure that the maintenance work is standardized and normalized, and to establish a maintenance record file, detailed records and analysis of the maintenance process, in order to [6] so that timely detection and problem solving .
Strengthen the daily inspection of equipment and troubleshooting work, through regular inspection, timely detection of abnormalities and potential problems of the equipment, take effective measures to solve, establish a perfect troubleshooting mechanism, rapid positioning and treatment of equipment failures, to ensure that the timely recovery of the equipment and the normal operation of the [7] turn.
In order to ensure the effective application of CNC machining technology in machining, the introduction of intelligent maintenance management system can realize the real-time monitoring of the state of the equipment and predictive maintenance, can be based on the equipment’s operating data and historical fault information, predict the maintenance needs of the equipment and the risk of failure, and formulate the maintenance plan and processing measures in advance, thus enhancing the efficiency and accuracy of equipment maintenance.
CNC machining technology in machining development trend
1. Intelligent CNC system
With the rapid development of artificial intelligence, big data and other advanced technologies, the intelligent CNC system is becoming an important development direction of CNC machining technology. The intelligent CNC system is able to realize the intelligence and automation of the machining process through learning, optimization and self-adjustment, and automatically selects the optimal machining parameters, tool paths and machining strategies according to the requirements of the machining task, so as to improve machining accuracy, efficiency and stability.
In addition, the intelligent CNC system can also realize seamless integration with other intelligent manufacturing systems, providing enterprises with more intelligent and flexible production solutions.
2. High-precision and high-efficiency composite processing technology
At this stage, the industry market for product quality and production efficiency requirements continue to improve, high-precision and high-efficiency composite machining technology has become one of the development trends of CNC machining technology.
Through the integration of a variety of machining methods, optimize the machining process and improve the performance of the machine tool and other means to achieve high precision and high efficiency at the same time.
Such as five-axis linkage [8] dynamic machining technology, high-speed cutting technology and other applications can not only improve the machining accuracy and surface quality, but also significantly improve the processing efficiency and shorten the production cycle.
3. Green manufacturing and energy saving and emission reduction
With the strengthening of environmental protection awareness and the depth of the sustainable development strategy, the implementation of green manufacturing and energy saving and emission reduction has become an important development model in the field of machining.
CNC machining technology is increasingly using environmentally friendly, renewable or recyclable materials to reduce the waste generated in the machining process and reduce the burden on the environment.
In addition, CNC machining equipment is moving in a more energy-efficient and efficient direction, and the application of new energy-saving equipment can significantly reduce energy consumption in the machining process, and reduce the emission of waste gas, wastewater and other pollutants generated during the machining process through the use of advanced emission control technology and equipment to reduce the pollution of the environment.
Conclusion
The application of CNC machining technology not only significantly improves the precision and efficiency of machining, but also provides a practical solution for the processing of glass transparent parts and other complex parts, making the machining process more intelligent, and automated, reducing the frequency of manual intervention and error rate, and further improving production efficiency and product quality.
At present, the application of CNC machining technology in machining has achieved remarkable results, in the future development process, but also need to intelligent CNC systems, high-precision composite machining technology, energy-saving and emission reduction processing mode as the main direction of development, to further expand the application of CNC machining technology in the field of machining, so as to promote the sustainable development of the machining industry.